Did you know that over one million organizations across 170+ countries are ISO 9001:2015 certified? This highlights the importance of understanding ISO 9001 clauses 2015 to ensure smooth compliance and operational efficiency. making it the most widely recognized quality management standard worldwide? By embedding quality management into daily operations, organizations can reduce waste, enhance efficiency, and gain a competitive edge in their industry. By implementing structured quality processes, companies can reduce errors, improve resource utilization, and strengthen overall business resilience.
Whether you're in manufacturing, healthcare, or any other industry, understanding the clauses of ISO 9001:2015 is essential for optimizing operations, enhancing customer satisfaction, and achieving certification. This blog provides a deep dive into each clause, breaking down its significance, impact on your business, and actionable steps to ensure seamless compliance.
Introduction to the Key Clauses of ISO 9001:2015
ISO 9001:2015 is an internationally recognized standard that outlines the criteria for a Quality Management System (QMS). It is designed to help organizations consistently provide products and services that meet customer and regulatory requirements. Effectiveness levels across ISO 9001:2015 clauses vary, highlighting strengths and areas for improvement. The infographic below offers a snapshot of average clause effectiveness, providing actionable insights to help your organization benchmark performance and focus on priority improvements.
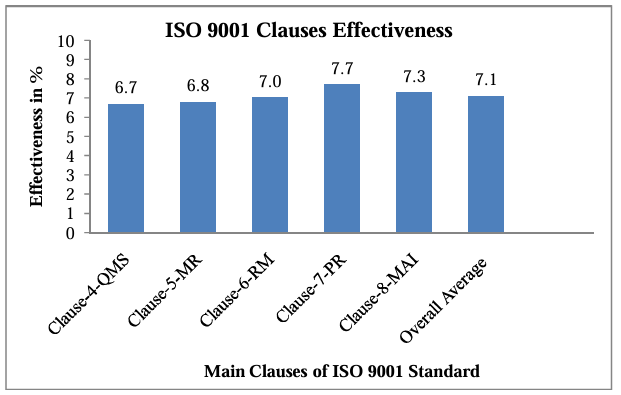
The standard consists of 10 clauses that provide a structured approach to quality management. Let's take a closer look at these clauses to understand their role in building an effective Quality Management System (QMS).
- Clause 1: Scope: This clause defines the applicability of ISO 9001:2015. It states that the standard applies to organizations of all sizes and industries that want to improve customer satisfaction, maintain regulatory compliance, and enhance operational efficiency.
- Clause 2: Normative References: This clause refers to ISO 9000:2015, which provides fundamental concepts, principles, and terminology related to quality management systems. Organizations are encouraged to refer to this document for additional guidance to ensure a deeper understanding of quality-related terms and concepts.
A clear scope and reference framework streamline ISO 9001:2015 implementation, improving efficiency and compliance. By aligning processes with industry standards, businesses boost operational effectiveness and customer trust. To build upon this strong foundation, it is essential to understand the precise terminology used in ISO 9001:2015. Clause 3: Terms and Definitions provides a structured overview of key terms, ensuring uniformity and clarity in their application throughout the organization.
Clause 3: Terms and Definitions
Mastering key terms in ISO 9001:2015 is essential for a smooth implementation process, ensuring uniform understanding across all departments and stakeholders. A clear grasp of these definitions helps prevent misinterpretations, enhances compliance, and streamlines integration into existing business processes.
Important Definitions:
- Quality Management System (QMS): A structured system for managing quality policies, processes, and objectives.
- Risk-Based Thinking: An approach that integrates risk awareness into strategic planning and decision-making.
- Nonconformity: A failure to meet a specified requirement in a process or product.
- Corrective Action: Steps taken to eliminate the cause of a detected nonconformity and prevent recurrence.
- Preventive Action: Measures taken to anticipate potential issues and prevent them from occurring.
Having a clear understanding of key terms in ISO 9001:2015 ensures consistency and clarity across an organization’s QMS. Proper definitions help in maintaining compliance and minimizing misinterpretations. With these fundamental terms in place, the next step is to explore Clause 4: Context of the Organization, which focuses on aligning the QMS with business objectives.
Clause 4: Context of the Organization
Recent assessments show that Clause 4 and Clause 5 have effectiveness scores below 70%, highlighting challenges in aligning quality objectives with strategic goals and leadership engagement. Strengthening these areas is crucial for building a resilient QMS and ensuring leadership actively drives quality initiatives. This clause requires organizations to analyze their internal and external environment to establish a strong foundation for their QMS. Understanding the broader business context helps in aligning quality objectives with strategic goals.
Key Aspects:
- Understanding Internal and External Issues: Organizations must assess market trends, customer expectations, regulatory requirements, economic factors, and technological advancements.
- Defining Interested Parties: Identify stakeholders such as customers, suppliers, employees, investors, and regulatory bodies, ensuring their needs and expectations are met.
- Establishing the Scope of the QMS: Define which processes, departments, and locations are covered under the QMS to avoid ambiguity in implementation.
- Process Approach: Organizations must map out their core and supporting processes to ensure consistency and efficiency.
A successful Quality Management System (QMS) requires a well-defined relationship between stakeholders, leadership objectives, and external business factors. The infographic below visualizes these connections, highlighting the role of leadership in aligning organizational goals with ISO 9001:2015 requirements. By understanding these interdependencies, organizations can enhance QMS effectiveness and strategic alignment.
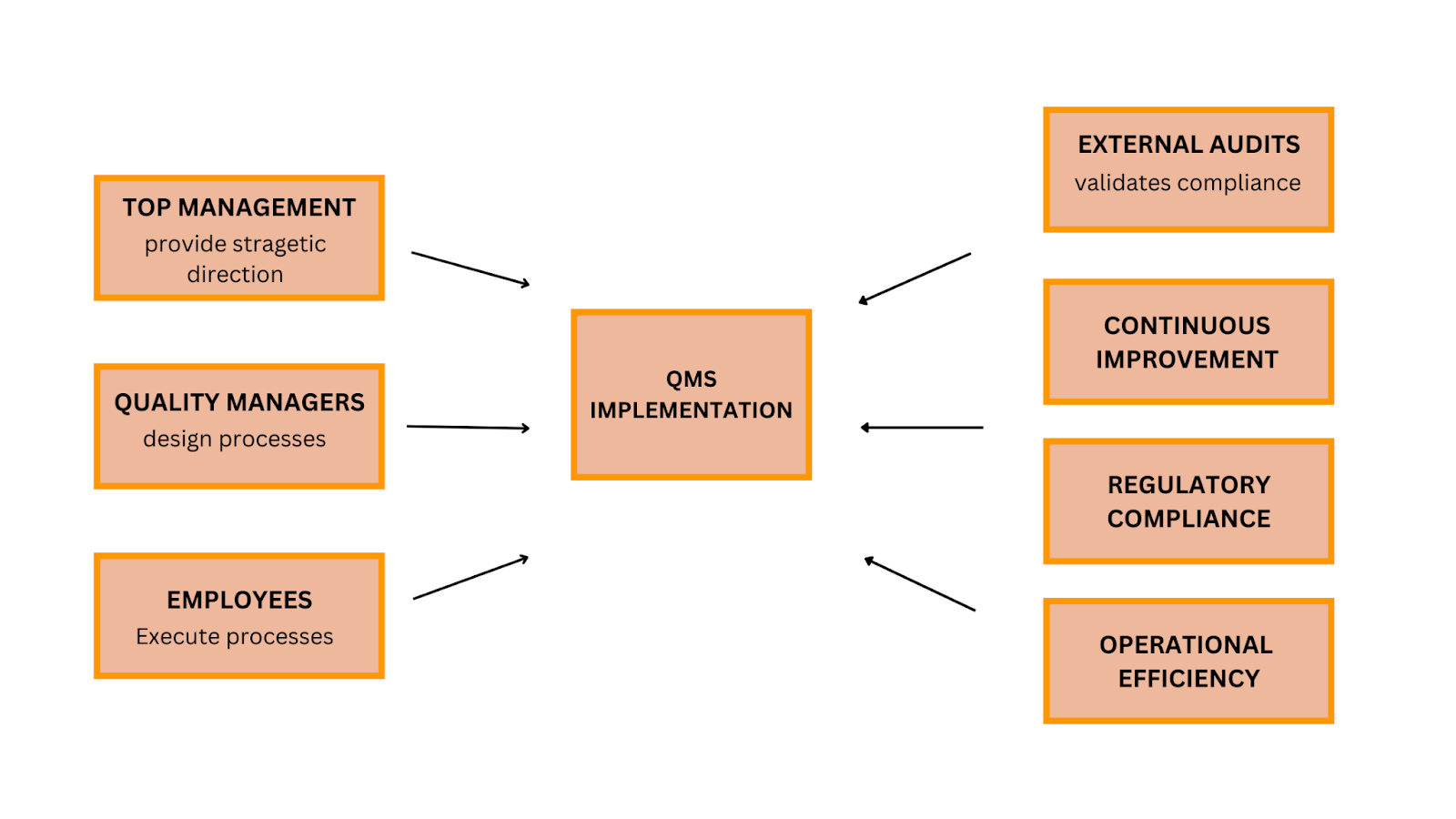
For a deeper understanding of how to define your QMS scope, check out our dedicated blog: Determining the Scope of the Quality Management System according to ISO 9001:2015.
With the scope clearly defined, the next step is to ensure strong leadership commitment. This is covered in Clause 5: Leadership, where top management plays a critical role in fostering a culture of quality.
Clause 5: Leadership
Strong leadership is essential in effectively implementing ISO 9001 clauses 2015. Management must engage with the QMS, ensuring alignment with business objectives and customer expectations.
Leadership Responsibilities:
- Defining and Communicating the Quality Policy: Leadership must ensure the policy aligns with business goals and is understood across all levels.
- Assigning Roles and Responsibilities: Clear accountability and authority improve efficiency and effectiveness.
- Promoting a Culture of Continuous Improvement: Engaging employees in quality initiatives and ensuring alignment with business objectives.
- Customer Focus: Leaders must ensure customer satisfaction is a priority in decision-making and process improvements.
Leadership commitment is key to embedding quality at all levels of an organization. When leadership actively supports the QMS, employees are more engaged, and quality objectives are achieved efficiently. With strong leadership in place, the next step involves Clause 6: Planning, which ensures that risks and opportunities are identified and addressed proactively.
Clause 6: Planning
Risk-based thinking is a key principle of ISO 9001:2015, requiring organizations to identify potential risks and opportunities that could impact their QMS. This clause emphasizes structured planning to ensure quality objectives are set and achieved effectively. By integrating risk management into planning, organizations can enhance resilience, minimize disruptions, and drive continuous improvement.
Key Requirements:
- Identifying Risks and Opportunities: Organizations must assess potential disruptions and advantages within their operational environment.
- Setting Quality Objectives: These should be measurable, realistic, and aligned with business goals. Organizations must also plan how to achieve these objectives.
- Developing Action Plans: Addressing risks and opportunities ensures consistent quality performance and prevents process failures.
- Change Management: Organizations must evaluate and manage changes that impact quality processes.
Planning is the foundation of an effective QMS, ensuring risks are mitigated and objectives are met. However manual planning can be time-consuming and prone to errors.
With BPRHub, you can automate planning, track compliance in real time, and ensure seamless alignment with ISO 9001 clauses 2015. Ready to simplify your QMS planning? Explore BPRHub today.
Once planning is established, it’s crucial to focus on the resources needed to support it. This leads us to Clause 7: Support, which covers the infrastructure, workforce, and knowledge management essential for QMS success.
Clause 7: Support
Among all the clauses, Clause 7 has the highest effectiveness score at 77%, reflecting strong implementation in resource allocation, training, and infrastructure, especially in product and production-oriented areas. This underscores the importance of well-structured support systems in maintaining QMS success. Ensuring compliance with ISO 9001 clauses 2015 requires continuous investment in resources and training, driving long-term quality improvements.
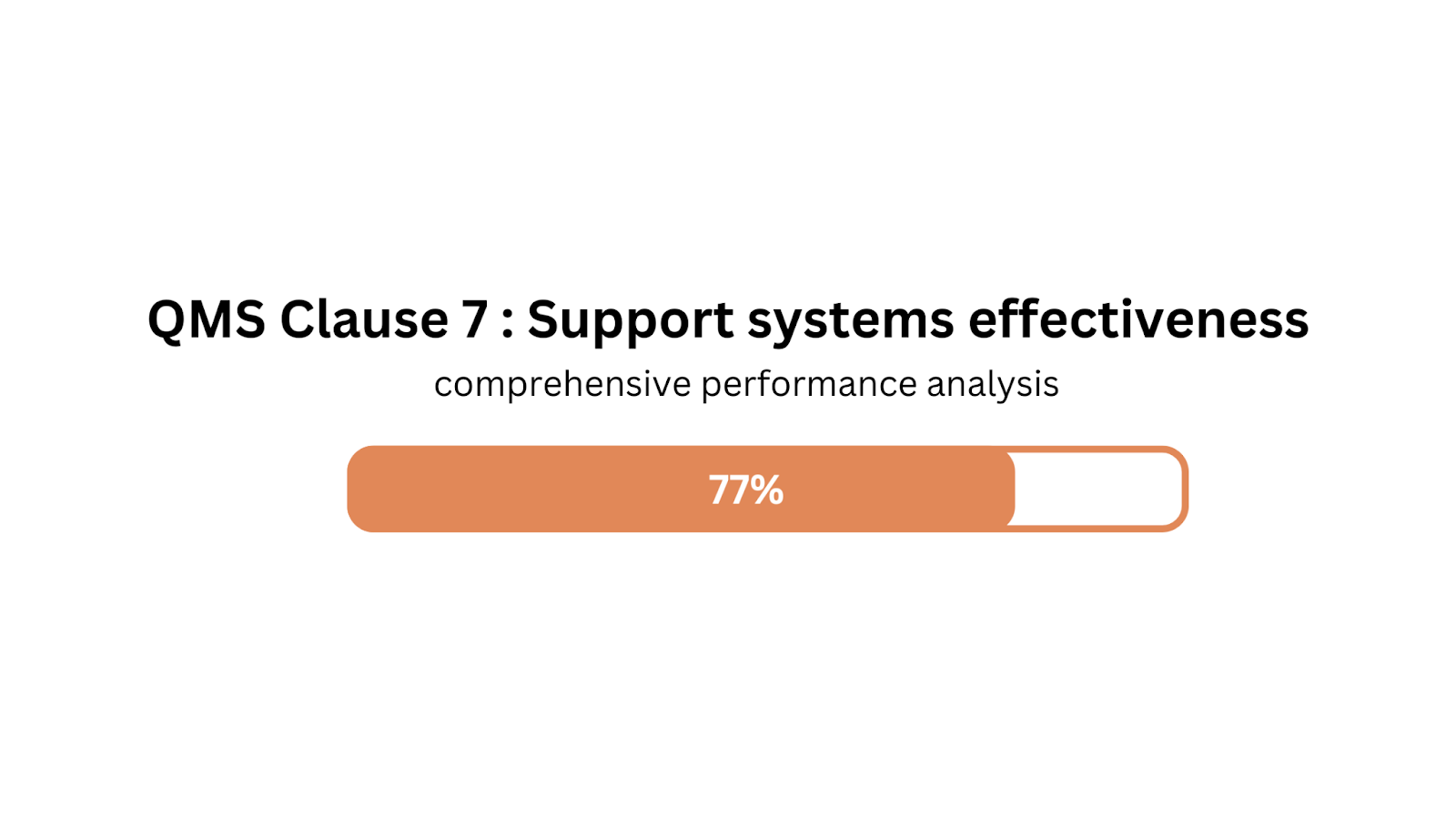
Areas Covered:
- Human Resources: Employees must be competent, trained, and equipped to carry out quality-related tasks effectively.
- Infrastructure & Work Environment: Ensuring facilities, equipment, and technology support quality goals and comply with safety regulations.
- Knowledge Management: Organizational knowledge must be documented, maintained, and easily accessible to relevant personnel.
- Communication: Effective internal and external communication ensures alignment and clarity of quality objectives.
- Documented Information: Organizations must control and maintain documents related to the QMS for consistency and accountability.
Providing the right resources and infrastructure is crucial for maintaining an effective QMS. Organizations that invest in strong support mechanisms lay the foundation for operational excellence. With proper support in place, the focus shifts to Clause 8: Operation, which ensures the consistent execution of quality processes.
Clause 8: Operation
This clause ensures that planned processes are executed efficiently to meet product and service requirements while maintaining strict quality control standards. Effective execution minimizes errors, enhances productivity, and ensures compliance with industry standards. Adhering to ISO 9001 clauses 2015 helps organizations maintain consistency in operations, reduce waste, and improve overall quality outcomes.
Key Focus Areas:
- Operational Planning and Control: Standardizing processes to prevent defects and deviations.
- Design and Development: Establishing a structured approach to developing new products and services that meet quality specifications.
- Supplier Management: Evaluating, monitoring, and controlling external providers to ensure quality and reliability.
- Production and Service Provision: Ensuring processes are implemented in controlled conditions to maintain quality standards.
- Nonconforming Outputs: Organizations must have a system in place to identify and control nonconforming products or services.
Operational control ensures that products and services meet quality requirements while adhering to regulatory standards. Ensuring efficiency in operations strengthens the QMS and enhances customer satisfaction. Next, we look at Clause 9: Performance Evaluation, which emphasizes the importance of monitoring and measuring QMS effectiveness.
Clause 9: Performance Evaluation
Regular monitoring and evaluation of processes are crucial under ISO 9001 clauses 2015. By tracking performance, organizations can identify gaps and continuously improve their QMS. Organizations must measure, monitor, and analyze their QMS effectiveness to drive continual improvement.
Performance Assessment Methods:
Evaluating performance is key to maintaining a strong QMS and ensuring continuous improvement. The following methods provide essential insights into effectiveness and areas for enhancement.
- Customer Satisfaction Monitoring: Gathering and analyzing customer feedback to enhance quality and service.
- Internal Audits: Conducting periodic audits to identify compliance gaps and areas for improvement.
- Management Reviews: Top management must periodically evaluate the QMS performance and make informed decisions for improvement.
- Data Analysis: Organizations must collect, analyze, and evaluate data related to QMS effectiveness to make data-driven decisions.
Continuous evaluation of performance metrics helps organizations identify areas for improvement and maintain compliance with ISO 9001:2015. Monitoring ensures the QMS remains effective and responsive to changing needs. The final stage, Clause 10: Improvement, focuses on creating a sustainable culture of continuous enhancement.
Clause 10: Improvement
Continuous improvement drives long-term success and adaptability in an evolving business environment. By refining processes, eliminating inefficiencies, and embracing innovation, organizations can maintain high-quality standards and stay competitive. ISO 9001:2015 promotes proactive improvements, helping businesses tackle challenges while boosting customer satisfaction and operational efficiency. Following ISO 9001 clauses 2025 ensures organizations remain aligned with evolving quality standards, reinforcing a culture of excellence and continuous growth.
Improvement Strategies:
- Addressing Nonconformities: Organizations must take corrective actions to prevent recurring issues and improve processes.
- Process Optimization: Refine workflows, eliminate inefficiencies, and integrate automation for higher efficiency.
- Innovation and Adaptation: Implementing new technologies and methodologies to enhance operational excellence.
- Corrective and Preventive Actions: Ensuring identified issues are addressed systematically with proactive measures to prevent recurrence.
Improvement is the backbone of a strong QMS. Organizations that proactively identify nonconformities and enhance their processes remain competitive and compliant. By implementing all the clauses effectively, businesses can achieve full ISO 9001:2015 certification and sustain long-term quality excellence.
How BPRHub Simplifies Compliance
Implementing ISO 9001:2015 successfully requires a structured approach, from planning and operation to evaluation and continuous improvement. To visualize this journey, the infographic below highlights the key stages of a Quality Management System (QMS) and how BPRHub supports each phase.
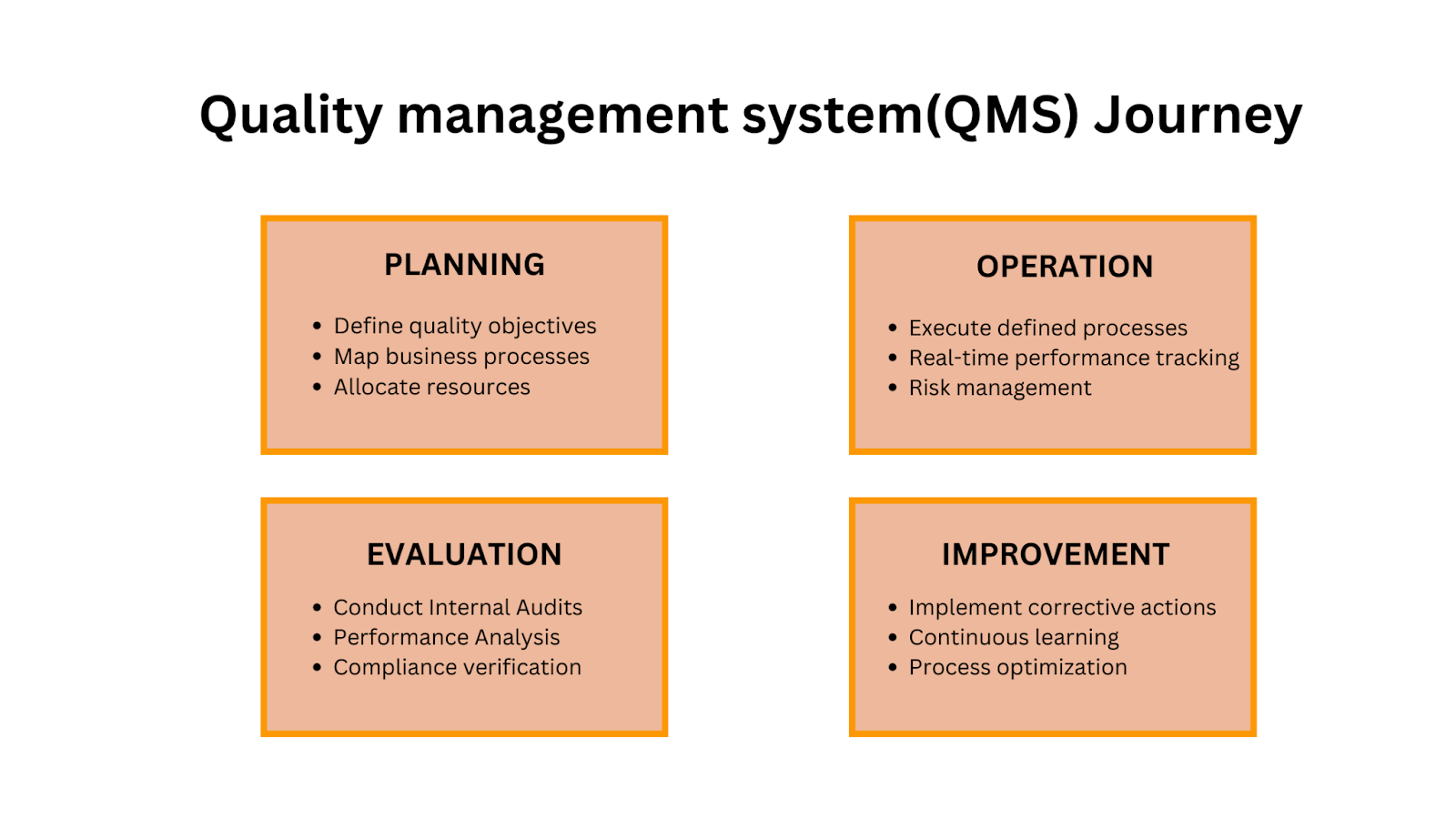
Navigating ISO 9001 clauses 2015 can be challenging, but BPRHub simplifies the process. Our platform automates workflows, provides real-time insights, and ensures smooth certification for manufacturing companies.
- Automate workflows for compliance tasks, reducing manual effort and errors.
- Gain real-time insights with live data to support informed decision-making.
- Optimize production processes, ensuring greater efficiency and reduced downtime.
- Ensure smooth ISO 9001 certification with pre-designed documents and compliance tracking tools.
Achieving ISO 9001 certification requires meticulous planning, adherence to compliance standards, and effective tracking of processes. With the right tools and structured workflows, businesses can simplify certification and maintain long-term quality excellence. By leveraging BPRHub, organizations can ensure seamless implementation, reducing manual efforts and enhancing operational efficiency.
Need assistance in implementing ISO 9001:2015 effectively? Let BPRHub take the complexity out of compliance. From automated workflows to real-time tracking, we help you stay ahead with minimal effort. Request a demo to see how BPRHub can make ISO 9001 certification easier than ever.
FAQs
1. What is the purpose of ISO 9001:2015?
ISO 9001:2015 provides a framework for organizations to establish a Quality Management System (QMS) that ensures consistent product and service quality, regulatory compliance, and customer satisfaction.
2. Why is understanding the clauses of ISO 9001:2015 important?
Each clause defines a specific aspect of quality management, from leadership commitment to operational execution. Understanding them helps organizations implement and maintain a successful QMS.
3. How does Clause 4 (Context of the Organization) impact QMS implementation?
Clause 4 requires organizations to assess internal and external factors influencing their QMS, ensuring that quality objectives align with business strategy and stakeholder expectations.
4. What role does leadership play in ISO 9001 compliance?
Clause 5 emphasizes the importance of leadership in establishing a quality-driven culture, setting clear objectives, and ensuring QMS integration into daily operations.
5. What are the key challenges in implementing ISO 9001:2015?
Common challenges include aligning QMS processes with business objectives, maintaining consistent documentation, conducting internal audits, and ensuring continuous improvement.
6. How can organizations improve their performance evaluation under Clause 9?
Organizations should use customer feedback, internal audits, KPIs, and management reviews to measure and enhance QMS effectiveness.
7. What is the significance of Clause 10 (Improvement)?
Clause 10 focuses on continuous improvement, ensuring that businesses address nonconformities, enhance efficiency, and adapt to changing quality requirements.
8. How can ISO 9001:2015 compliance be simplified?
Using automated QMS tools, structured workflows, and real-time monitoring solutions can streamline compliance and reduce manual effort.