as ISO standards, OSHA rules, FDA guidelines, and environmental laws. For each of these requirements, thorough paperwork is needed, such as:
- Standard Operating Procedures (SOPs) : These are detailed rules for how to carry out a task.
- Quality Control Records : These are logs that keep track of how consistent and good the products are.
- Audit reports : The records of checks done by people inside and outside the company.
- Safety and Training Documents: Proof that workers were trained and that safety steps were taken in the workplace.
- Supplier and Material Certifications: These show that the raw materials meet the rules set by the government.
Every compliance document would adhere to particular rules specified by the framework. You have the option of implementing several frameworks at once or selecting only one, such as ISO 27001, SOC 2, GDPR, PCI DSS, or HIPPA.
The audit documentation varies depending on the standards, regulations, and needs of each law, including California Proposition 65, EU REACH, EU RoHS, SCIP, Conflict Minerals, IMDS, EU MDR (Medical Device Regulations), and so forth.
If your organisation is in the healthcare industry, for instance, your compliance documentation should be in line with HIPAA regulations and the documentation for HIPAA compliance, with an emphasis on the internal controls you have in place to safeguard PHI.
The right paperwork & updated documentation are major credibility factors in the compliance industry. It becomes easy for a business to show & track that it is following the rules, staying out of trouble with the law, and running the operations smoothly. Manual paperwork, on the other hand, can take a long time, be mistake-prone, and be hard to keep track of.
Navigating Industry-Specific Compliance Documentation
Different manufacturing sectors have unique product compliance requirements, each demanding specific documentation to meet industry regulations. Below are the key compliance documents needed for various manufacturing industries:
1. Pharmaceutical & Medical Device Manufacturing
- Good Manufacturing Practices (GMP) Documentation – Compliance with FDA and WHO regulations.
- Batch Records (BPRs) – Documentation of each production batch.
- Drug Master File (DMF) – Detailed information about the production process, raw materials, and quality control.
- FDA 21 CFR Part 11 Compliance Records: Records related to electronic records and signatures
2. Food & Beverage Manufacturing
- Hazard Analysis and Critical Control Points (HACCP) Plan – Ensures food safety by identifying potential hazards.
- Food Safety Management System (FSMS) Reports – Compliance with FSSAI, FDA, or international food safety standards.
- Supplier and Ingredient Certifications – Proof of quality and safety of raw materials used, ISO 22000, FSSC 22000, etc.
- Recall & Traceability Records – Documentation for product recalls, if required.
3. Automotive & Aerospace Manufacturing
- ISO 9001, AS9100 & IATF 16949 Certifications – Quality management system documents.
- Material Safety Data Sheets (MSDS) – Information about hazardous substances used in production.
- Failure Mode and Effects Analysis (FMEA) Reports – Documentation of potential failures and preventive measures.
- Product Testing & Inspection Reports – Verifications ensuring products meet industry safety standards.
4. Electronics & Semiconductor Manufacturing
- Bill of Materials (BOM): Lists of components used in products.
- RoHS (Restriction of Hazardous Substances) Compliance – Ensures hazardous substances are not used.
- REACH (Registration, Evaluation, Authorization of Chemicals) Compliance – Required for European market entry.
- UL Certification & Testing Reports – Safety compliance for electrical components.
- Process Validation Reports – Ensures consistent quality and performance of electronic components.
5. Chemical & Petrochemical Manufacturing
- Environmental Impact Assessments (EIA) – Documents regulatory compliance for pollution control.
- OSHA Safety Reports – Ensures workplace safety for employees handling hazardous materials.
- SDS (Safety Data Sheets) – Mandatory for chemical handling and transportation.
- Emission & Waste Disposal Records – Ensures compliance with environmental protection laws.
These examples highlight the diverse compliance documentation requirements across industries. It's crucial for manufacturers to understand the specific regulations and standards applicable to their operations and implement robust audit documentation systems to ensure compliance.
Key Challenges With Manual Documentation In Manufacturing Compliance
Manufacturers face a number of problems when they don't have a well-organized method for keeping records, such as:
- Time Consumption : Employees look for papers or fill out forms for hours on end.
- Human Errors - Data that is missing or wrong can happen in paper-based systems or digital files that are not organized.
- Compliance Risks: Not having enough paperwork can lead to fines from the government or delays in production.
- Inefficiency in Audits - Getting ready for audits is stressful when the process isn't organized.
The inability to keep track of each batch's production records, backdated documents, lost records, and acquiring a government document that needs to be legalised are all serious documentation problems & for the compliance industry too.
For example: A data breach in 2017, concerning loss of around 150 million people’s personal information, cost Equifax around $575 million.
Types of Compliance Documents Every Manufacturer Needs
Manufacturing compliance requires maintaining various types of documentation, each serving a specific purpose in your quality management system:
- Quality Management System (QMS) Documents: These documents describe your organization's quality management system, including policies, procedures, work instructions, and forms. Examples include:
- Quality Manual: The cornerstone document outlining your company's quality management system and approach to compliance
- Standard Operating Procedures (SOPs): Step-by-step instructions for routine operations that ensure consistency and product compliance
- Work Instructions: Detailed, task-specific guidance for operators performing specific processes
- Process Flow Charts: Visual representations of workflows that help identify control points and responsibilities
- Forms and Templates: Standardized documents used for recording data.
- Production Records and Reports
- Batch Records: Documentation of each production batch, including material usage, equipment settings, and quality checks
- Non-conformance Reports: Documentation of product or process deviations and the corresponding corrective actions
- Equipment Logs: Records of equipment usage, maintenance, calibration, and validation
- Inspection Reports: Documentation of quality control inspections and tests.
- Training Records: These documents demonstrate that employees have received the necessary training to perform their jobs safely and effectively. Examples include:
- Training Plans: Outlines of training programs.
- Training Materials: Documents used in training sessions.
- Training Attendance Records: Proof that employees attended training.
- Audit Records: These documents record the results of internal and external audits, including findings, corrective actions, and preventive actions. Examples include:
- Audit Plans: Schedules and objectives for audits.
- Audit Reports: Summaries of audit findings.
- Corrective Action/Preventive Action (CAPA) Reports: Documentation of actions taken to address audit findings.
- Regulatory and External Documents
- Regulatory Submissions: Audit Documents submitted to regulatory bodies like FDA, EPA, or OSHA
- Certificates of Analysis: Quality confirmation documents that accompany raw materials or finished products
- Risk Assessments: Systematic evaluations of potential hazards and mitigation strategies
Managing this diverse array of documents manually is practically impossible without risking compliance gaps. This is why a structured system like BPR Hub becomes essential for modern manufacturers & their compliance process.
How Automated Solutions Help Streamlining Documentation ?
When manufacturers use a digital option to keep track of compliance paperwork, they can:
- Reduce Administrative Burden - Automating jobs that are done over and over again saves time and effort.
- Improved Accuracy: Having digital records in one place cuts down on mistakes and makes sure that all the data is consistent.
- Enhance Compliance Readiness – Audits and legal checks are easier to do when records are easy to get to and up to date.
- Boost Productivity : Make the employees & system more productive by letting them focus on important jobs instead of paperwork.
Simplifying Documentation With BPR Hub
BPR Hub is designed to help manufacturers overcome the problems they face regarding their documentation on a daily basis and in the long term for legal compliance. It provides a complete and easy-to-use way to keep all papers related to compliance in order and easy to find. This is what BPR Hub does that's different:
1. Centralized Document Management
With BPR Hub, you can keep all of your operations, administrative & compliance-related files in one safe place. No more looking for things in filing boxes or digital folders that are all over the place. Your team can get access to important files from anywhere at any time with a cloud-based system.
2. Automated Workflows
Tasks that need to be done over and over, like checking for product compliance, document review, and version tracking, can now be done automatically. This makes sure that documentation methods are always the same and cuts down on the work that needs to be done by hand.
3. Real-Time Collaboration
Multiple people on a team can work together on paperwork at the same time, making changes and updates without any problems. This gets rid of the chance of having old or duplicate files.
4. Compliance Tracking & Alerts
With automatic alerts for compliance needs, BPR Hub helps you stay ahead of deadlines. The system makes sure you never miss a vital deadline, whether it's an upcoming audit or a document renewal.
5. Secure and Scalable Storage
When working with compliance paperwork, security is very important. BPR Hub gives encrypted cloud storage to keep private information safe. The system can also be expanded to meet the needs of businesses that are growing.
6. Audit-Ready Reporting
With BPR Hub, getting ready for an audit is no longer a rush at the last minute. With just a few clicks, the system makes reports that are ready for audits. This makes sure that checks and regulatory approvals go smoothly.
7. Version Control
The version control feature of Documentation Hub ensures that manufacturers always have access to the most up-to-date and approved documents. It automatically tracks workflow, maintains changes & updates made to the document chronologically, keeps all the historical records, and prevents unauthorized modifications, ensuring compliance with industry regulations. With real-time updates and audit-ready logs, BPR Hub's Documentation Hub eliminates the confusion of multiple document versions, streamlining collaboration and regulatory reviews.
Document Hub - The Control Center of All You Compliance Documentation Needs
BPR Hub provides a central repository where you can create, upload, and manage all compliance-related documents in one place.
To create a document, simply click on "Create Document", and a form will appear asking for the necessary details. After filling in the required information, click "Submit", and the document will be saved as "Draft".
The draft is then sent to the approver for review. Once approved, the document status updates to "Published", making it ready for use. This streamlined process ensures accuracy, compliance, and easy access to essential documentation.
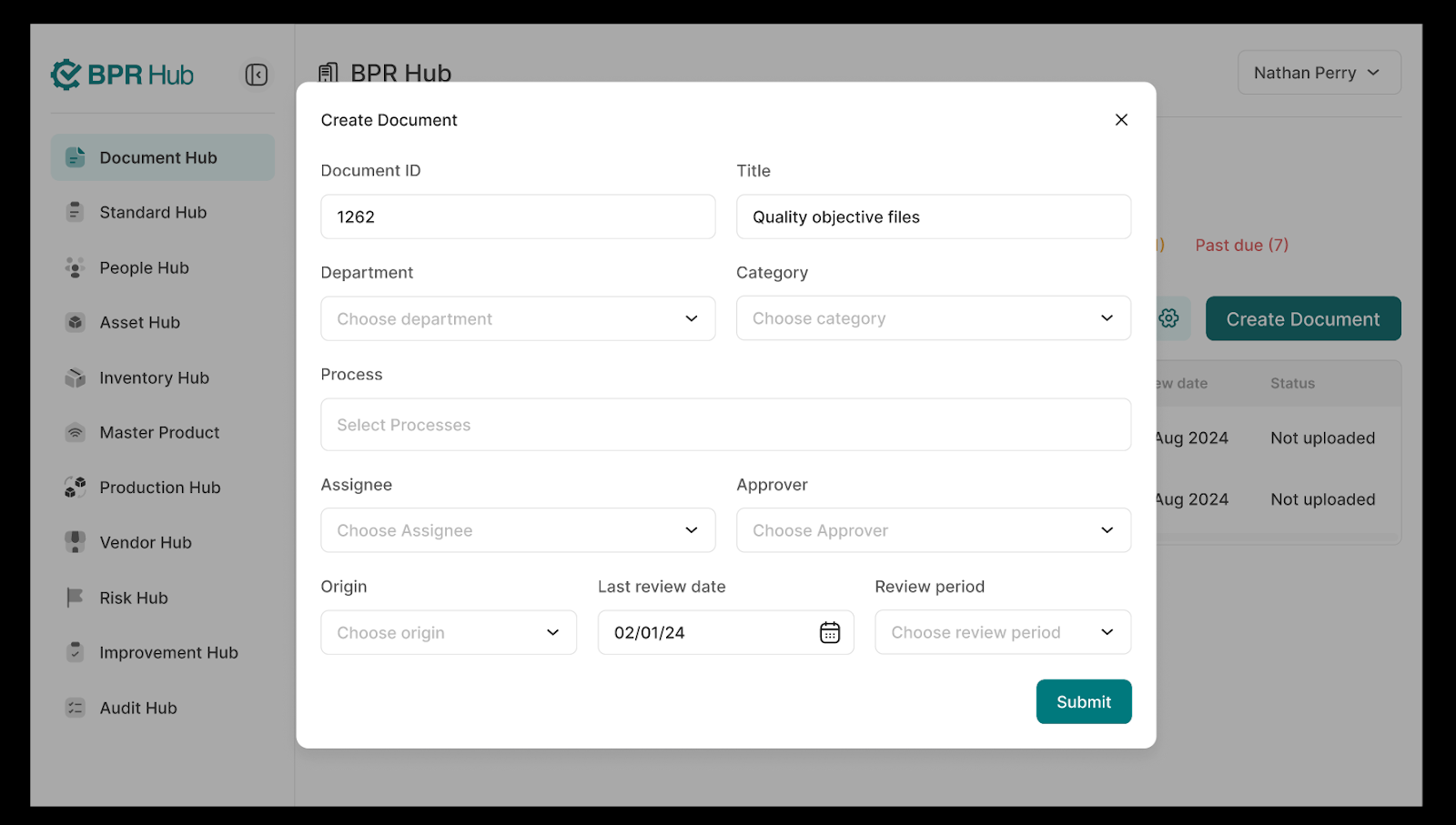
The Document Administration feature of BPR Hub's Documentation Hub allows you to manage your processes, departments and categories that you would be mapping your documents. Attaching processes, departments and categories to documents helps in referencing the document in other modules throughout the product. It has been designed keeping in mind the functionality to search through these documents, view the history & status of documents and much more.
Other features Making Document Hub Your Go-to-Solution
1. The Panel has a “Versions” tab that provides information on all the previous “Published” versions of the document, along with the option to download them.
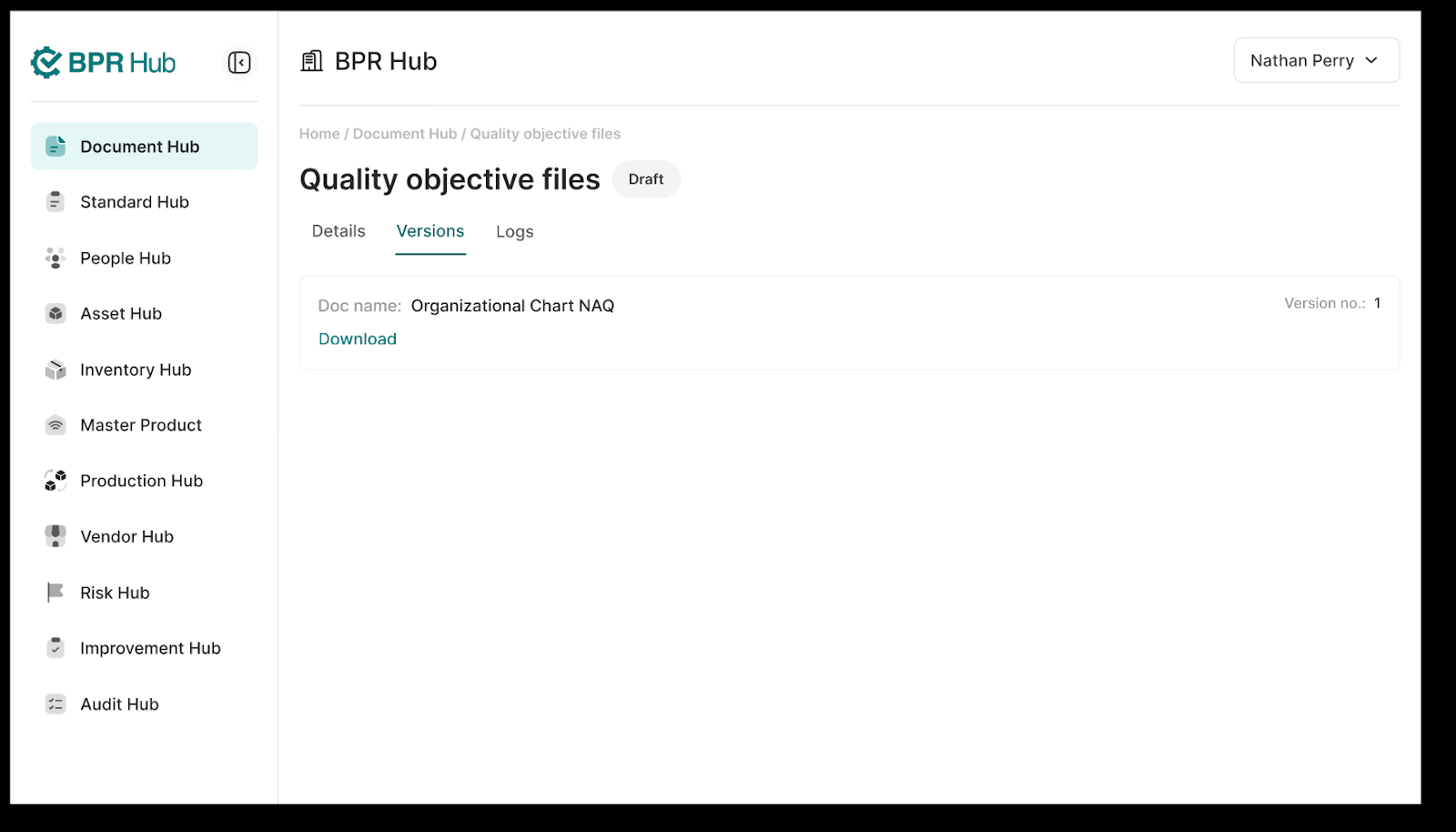
2. The “Details” tab shows all the details about this doc instance along with the option to edit them or delete the document instance entirely.
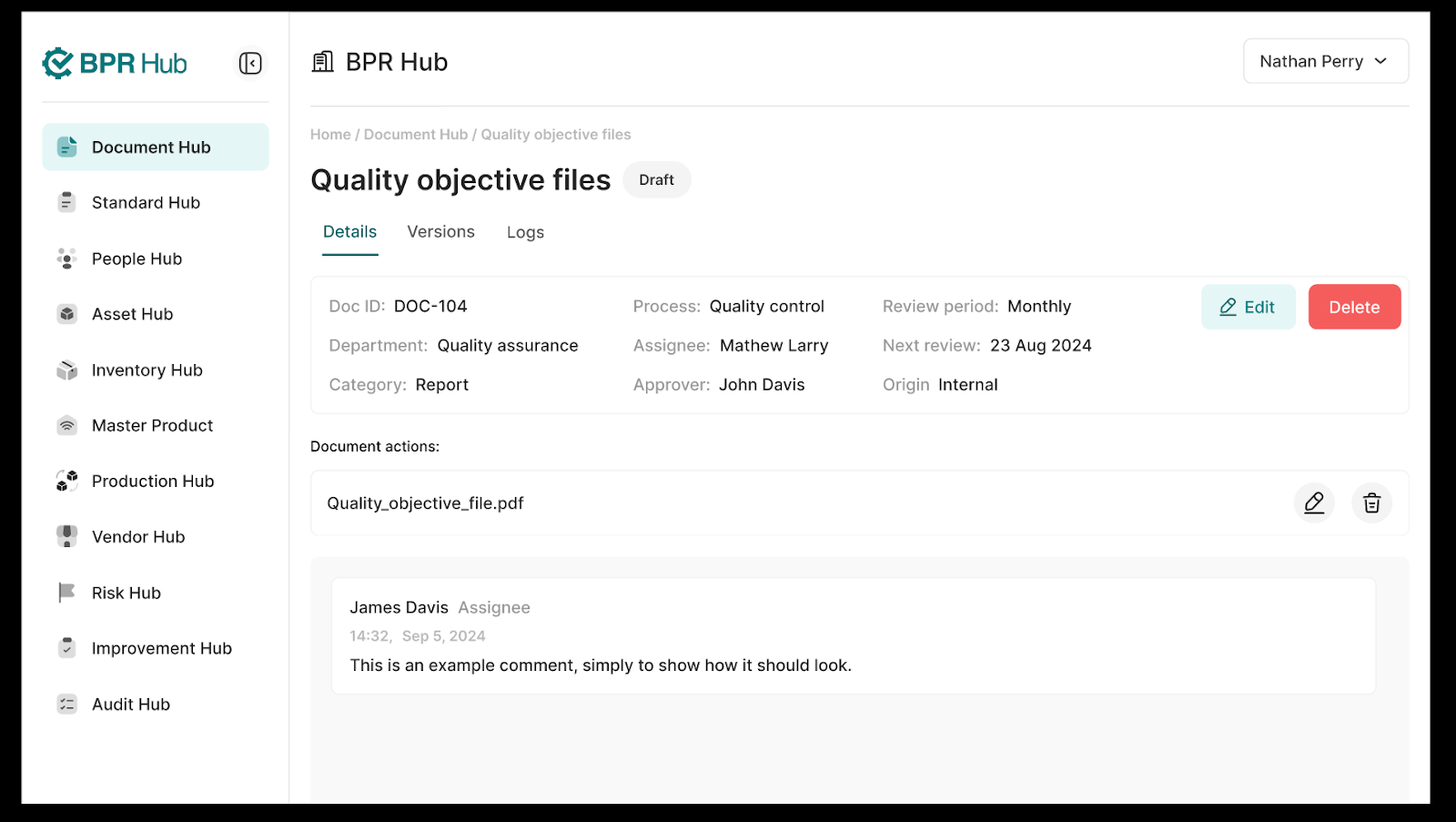
3. The “Logs” tab shows the chronological history of every action that was taken on this document instance. This includes edits to the details, status changes, approvals as well as comments added.
4. Option to upload an existing file
5. Option to create a new document from scratch using a “Word”-like inline editor
6. The comment system allows the assignees and approvers to communicate details / queries about the document asynchronously (equipped with an email notification system as well)
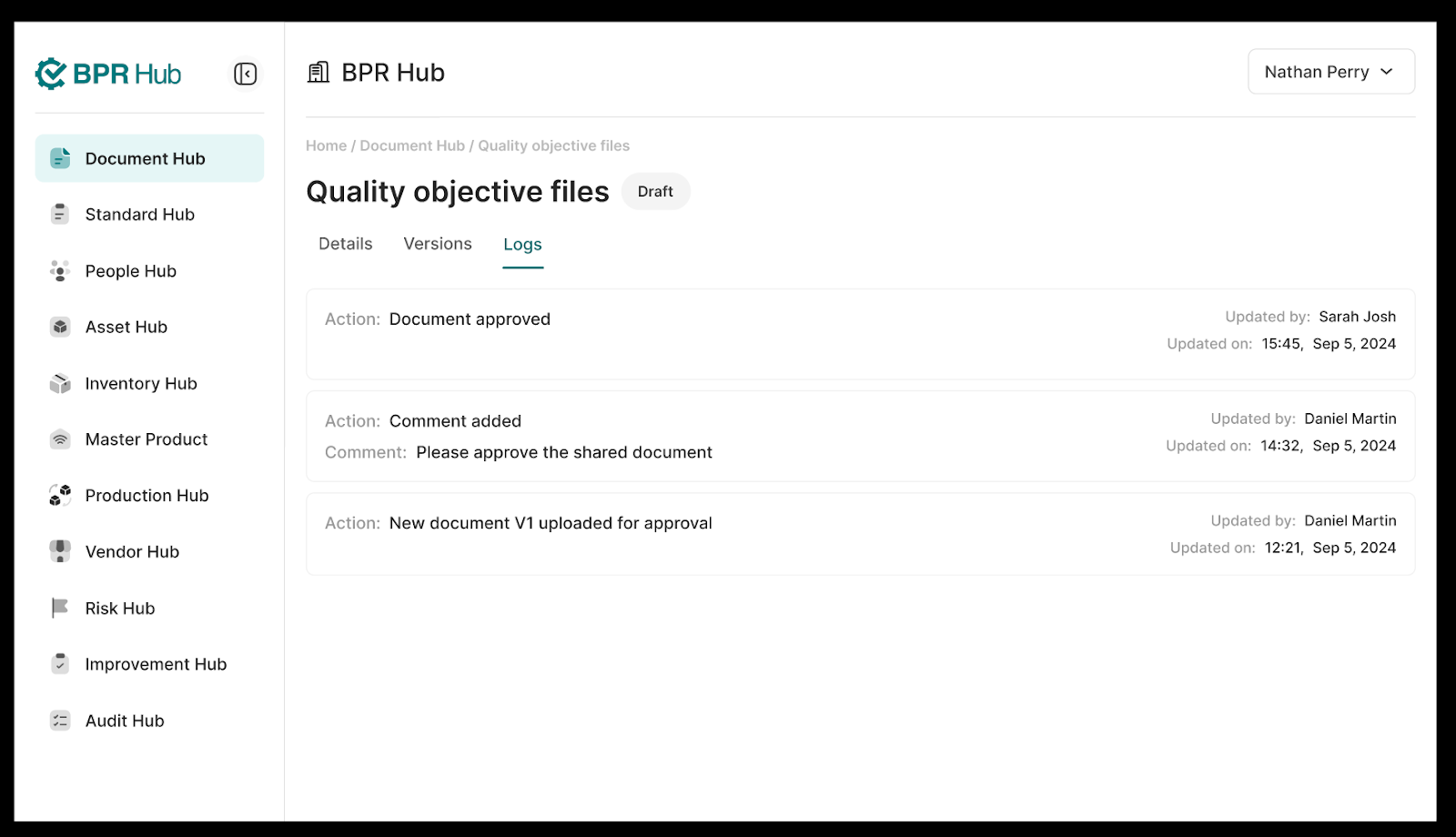
Best Practices in Documentation for Manufacturing Compliance
Effective compliance documentation ensures that manufacturers meet regulatory requirements, reduce risks, and improve operational efficiency. To ensure your documentation processes meet industry standards & is audit-ready, follow these practices :
- Standardization of Documents – Use a consistent format, naming conventions, and templates to ensure clarity and uniformity across all compliance records.
- Establish Clear Document Hierarchies: Define roles, responsibilities, and procedures for document creation, review, approval, and distribution.
- Implement a Centralized Document Management System: A centralized system, like BPR Hub, provides a single source for all compliance-related documents, simplifying access and version control.
- Regular Updates & Reviews – Compliance requirements evolve, so regularly update policies, SOPs, and regulatory documents to stay aligned with industry standards.
- Control Document Revisions: Implement a robust version control system to track changes, ensuring everyone works with the most current and approved versions. Clearly identify revisions and their effective dates.
- Automated Workflows – Implement automation for approvals, tracking, and notifications to minimize manual errors and improve efficiency.
- Audit-Ready Documentation – Maintain a well-organized system that allows quick retrieval of documents during compliance processes like inspections and audits, ensuring compliance readiness.
- Employee Training & Awareness – Ensure that all team members are trained in proper documentation practices to prevent inconsistencies and maintain accuracy.
- Data Security & Compliance – Protect sensitive compliance records through encryption, access controls, and secure backups to prevent unauthorized access or loss.
By following these best practices, manufacturers can streamline compliance processes, reduce regulatory risks, and improve overall operational efficiency.
Conclusion
Compliance documentation shouldn't slow down the production process in today's fast-paced world. A well-organized and automated system for paperwork makes things run more smoothly, lowers the risk of not following the rules, and lets companies focus on growth.
BPR Hub with its automated documentation offers the best way to make compliance documentation easier to find and use. With its centralized platform, automated workflows, real-time teamwork, and safe storage, it helps manufacturers make their compliance processes more accurate and faster.
When it comes to making legal paperwork easier, BPR Hub is the way to go. Start streamlining your paperwork right away, and you'll easily be able to handle your legal process.
Don’t let compliance documentation slow you down. Book a demo with BPR Hub today and discover how you can help you streamline your compliance documentation, reduce errors, and stay compliance ready!
Frequently Asked Questions (FAQs)
What types of documents can I manage with BPR Hub?
BPR Hub is designed to handle a wide range of compliance documents, including quality control records, training logs, SOPs, audit reports, calibration certificates, and more. Essentially, any document related to demonstrating and maintaining compliance can be managed within the platform.
Can BPR Hub integrate with my existing systems?
BPR Hub is designed with integration in mind. Depending on your existing systems and their APIs, we can explore integration possibilities to create a seamless flow of information. Contact us to discuss your specific integration needs.
What kind of support does BPR Hub offer?
We provide comprehensive support to our customers, including onboarding, training, and ongoing technical assistance. Our dedicated support team is available to answer your questions and help you get the most out of BPR Hub.
What industries can benefit from BPR Hub?
BPR Hub is designed for manufacturers across various industries, including pharmaceuticals, automotive, food processing, and electronics, ensuring smooth compliance process with industry-specific regulations.
How secure is my data in BPR Hub?
Data security is a top priority in every compliance process. BPR Hub utilizes robust security measures, including encryption, access controls, and regular backups, to protect your sensitive information. We also comply with industry best practices for data security and privacy.
Does BPR Hub help with audit preparation?
Absolutely! BPR Hub generates audit-ready reports and keeps compliance documentation organized, making audit preparations faster and stress-free.