Effective risk assessment is critical to ensuring a safe workplace, meeting regulatory standards, and maintaining operational efficiency in manufacturing environments. Whether you're managing a large factory or a smaller production unit, taking a proactive approach to identifying and mitigating risks is key to preventing incidents and improving productivity.
How you conduct risk assessments can significantly impact your organization, shaping everything from employee morale to operational costs and long-term resilience. A thorough and systematic approach ensures not only compliance but also fosters a culture of safety and efficiency.
In this guide, we’ll cover the crucial steps for conducting a risk assessment in manufacturing and demonstrate how BPRHub’s tools can simplify the process, enhance efficiency, and improve safety outcomes—all without adding complexity.
Importance of Risk Assessment in Manufacturing
Risk assessment isn’t just about avoiding accidents—it's about creating a safer, more efficient work environment that aligns with industry regulations. Here are some key benefits:
- Safer workplaces: Proactively identifying and addressing potential hazards creates a safer work environment. Regular risk assessments help spot dangers before they pose serious threats to employees' well-being. According to the U.S. Bureau of Labor Statistics, the manufacturing sector recorded approximately 330,000 non-fatal injuries in 2020.
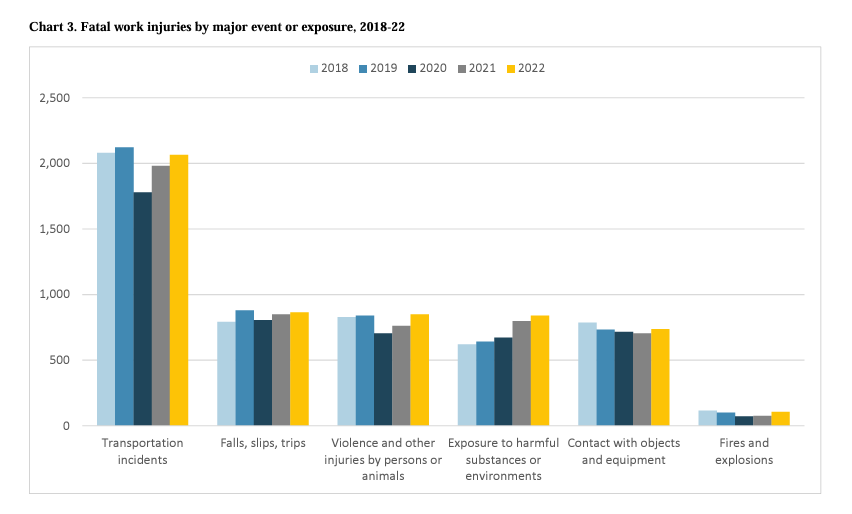
- Compliance with regulations: Staying compliant with safety regulations ensures your manufacturing operations meet industry standards, helping you avoid penalties and prioritize worker safety. The Occupational Safety and Health Administration (OSHA) provides guidelines on workplace safety that can help in maintaining compliance.
- Incident reduction: Mitigating risks early not only prevents small issues from escalating into major incidents but also reduces costs associated with workplace injuries. Effective risk management minimizes accidents, leading to lower medical expenses, downtime, and legal liabilities. The National Safety Council estimates that the total cost of workplace injuries in the U.S. exceeds $171 billion annually.
- Boosted productivity: A safe and hazard-free workplace improves overall productivity. When employees feel secure, they can focus better on their tasks, leading to more efficient operations and higher output.
- Employee empowerment: Involving workers in safety initiatives fosters a sense of responsibility and engagement. Empowered employees contribute to a safer workplace and are more likely to follow safety protocols diligently.
Conducting a thorough risk assessment in manufacturing is essential for maintaining a safe and compliant workplace. It helps ensure that potential hazards are identified and addressed while aligning with safety regulations. By prioritizing safety, you create a more efficient and empowered workforce.
Steps to Conduct a Risk Assessment
To ensure a safe and efficient manufacturing environment, conducting a proper risk assessment is crucial. It helps identify potential hazards, evaluate risks, and implement effective control measures.
Here’s a step-by-step guide to conducting a comprehensive risk assessment that can help prevent incidents and improve operational safety in your facility.
Step 1: Identify Potential Hazards
- Conduct Direct Observations: Assess equipment, processes, and working conditions to spot hazards firsthand.
- Consult Workers: Engage employees involved in daily operations to gather insights about potential risks that may not be obvious.
- Review Incident Reports: Analyze past incidents to identify trends or recurring issues.
We'll be diving into the details of common hazards, including biological, chemical, and physical risks, equipment malfunctions, and challenges related to heavy machinery and material handling, in the sections below.
Step 2: Evaluate the Risks
- Assess Severity: Consider the potential harm associated with each identified hazard.
- Determine Likelihood: Evaluate the probability of each hazard occurring.
- Prioritize Risks: By assessing both impact and probability, prioritize risks that require immediate action while identifying others needing ongoing monitoring.
Step 3: Implement Control Measures
With the risks assessed, implement appropriate control measures to minimize or eliminate them. Options include:
- Elimination: Completely remove the hazard from the workplace.
- Substitution: Replace hazardous materials or processes with safer alternatives.
- Engineering Controls: Modify equipment or the work environment to minimize risks, such as adding safety guards or improving ventilation systems.
- Administrative Controls: Change work procedures and practices to reduce exposure to hazards.
- Personal Protective Equipment (PPE): Provide necessary protective gear, such as gloves, helmets, or goggles.
A balanced approach that includes multiple types of control measures is often the most effective way to mitigate risks.
Step 4: Document and Communicate Findings
- Clear Documentation: Ensure all risk assessments are well-documented and easily accessible to all employees.
- Effective Communication: Clearly communicate findings to both workers and management, ensuring everyone understands the identified risks and control measures.
- Maintain an Updated Log: Keeping an updated log of assessments empowers teams to act quickly if new risks arise.
Step 5: Monitor and Review Regularly
Risk assessment is not a one-time activity; it requires regular reviews to:
- Verify Effectiveness: Regularly check that control measures are effectively mitigating identified risks.
- Identify New Risks: Monitor for any new risks emerging from changes in equipment, processes, or workforce dynamics.
- Update Control Strategies: Continuously adjust control measures to align with operational changes.
Continuous monitoring ensures that your risk management strategies evolve alongside your manufacturing processes.
Looking to simplify risk assessments? BPRHub makes it easy! Our platform automates everything from identifying risks to tracking them in real-time. Stay compliant, keep your team informed, and manage workplace safety effortlessly. Contact us today to see how BPRHub can streamline your risk management!
Types of Hazards in Manufacturing
In a manufacturing environment, hazards can come from various sources, such as:
Biological, chemical, and physical hazards:
- Exposure to harmful chemicals, gases, or biological agents can lead to serious health issues like respiratory problems, burns, or long-term illnesses.
- Physical hazards, such as extreme temperatures, excessive noise, or radiation, can cause injuries like heat stress, hearing loss, or radiation sickness.
- Proper safety protocols, protective equipment, and regular monitoring are essential to manage these risks effectively.
Biological, chemical, and physical hazards pose serious risks in many industries, emphasizing the need for strong safety protocols. In 2022, biological hazards caused over 550,000 deaths globally, mostly from communicable diseases, highlighting their impact in high-risk sectors like manufacturing and healthcare.
Chemical hazards are equally concerning, with the WHO reporting 2 million deaths and over 53 million disability-adjusted life years lost in 2019 due to exposure. Physical hazards, such as noise, vibration, and radiation, also remain significant threats, stressing the importance of comprehensive safety measures to protect workers' health.
Operational hazards:
- Malfunctioning or improperly maintained machinery can cause accidents, injuries, or production delays.
- Unsafe equipment handling, such as skipping maintenance checks or improper use, increases the risk of serious incidents.
- Regular inspections, routine maintenance, and thorough worker training are crucial for minimizing these risks.
Safety hazards:
- Improper use of tools or machinery, such as neglecting machine guards or safety locks, can result in severe injuries like cuts, fractures, or amputations.
- Lack of protective measures, such as failure to wear required PPE, puts workers at high risk for injuries.
- Ensuring workers follow safety guidelines and making protective equipment readily available are key to preventing such hazards.
By identifying and categorizing these hazards, you can implement targeted measures that enhance safety and compliance in your workplace. This proactive approach not only protects your employees but also fosters a culture of safety that benefits the entire organization.
Techniques for Risk Identification and Analysis
To conduct a thorough risk assessment, utilizing the right tools can significantly enhance your ability to identify and analyze potential hazards. Various methods are available that can aid in the systematic evaluation of risks, ensuring that no critical areas are overlooked.
Here are several effective tools that can streamline the risk identification and analysis process in your manufacturing environment:
- SWOT Analysis: This method involves identifying the strengths, weaknesses, opportunities, and threats within your operations. By analyzing these factors, you can gain insights into areas for improvement and potential risks.
- Failure Mode and Effects Analysis (FMEA): FMEA is a proactive approach that helps pinpoint potential failures in a process and evaluates their impact. This systematic analysis enables you to prioritize risks and implement effective controls before issues arise.
- Risk Assessment Checklists: Utilizing comprehensive checklists ensures that all aspects of safety are thoroughly considered during the assessment. These tools help standardize the evaluation process and ensure no critical elements are overlooked, promoting a safer work environment.
Enhancing Workplace Safety: Key Risk Control Methods
Once risks have been thoroughly evaluated, it is crucial to implement effective control measures to mitigate those risks. The choice of control methods will depend on the severity and nature of the identified hazards.
Here are several key strategies for controlling risks in the manufacturing environment:
- Elimination or Substitution: Remove the hazard entirely or replace it with a safer alternative. For example, replacing toxic chemicals with less harmful substances can significantly reduce exposure risks.
- Engineering Controls: Modify equipment or work environments to minimize risk, such as improving machine guards or enhancing ventilation systems.
- Administrative Controls: Change work procedures to reduce exposure to hazards, including revising workflows and increasing employee training.
- Personal Protective Equipment (PPE): Provide appropriate gear to protect workers from exposure to residual risks.
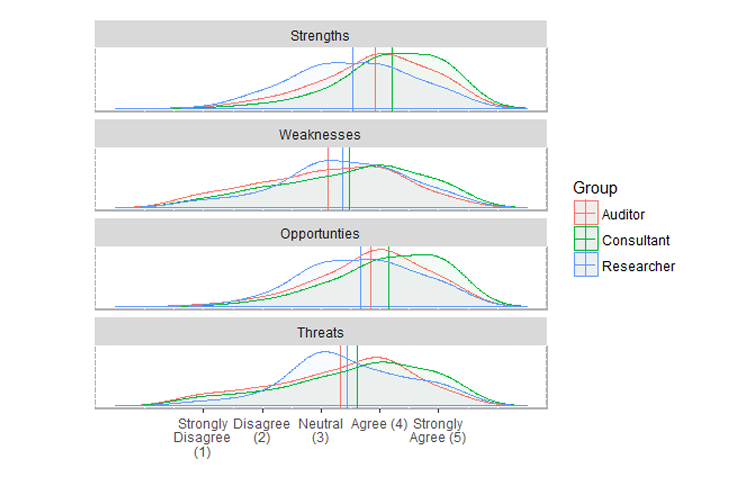
As illustrated in the above Figure, which shows the group response distribution by category, the perspectives of auditors, consultants, and researchers can vary significantly when evaluating strengths, weaknesses, opportunities, and threats.
This highlights the importance of collaborative input in conducting a thorough risk assessment. Each of these control methods plays a vital role in reducing hazards in the workplace. By integrating these strategies into your risk management plan, you can significantly enhance safety and compliance within your manufacturing operations.
Role of Continuous Training and Monitoring
Training employees on risk awareness and control measures is crucial for maintaining safety in manufacturing. Continuous training helps workers stay proactive and apply safety measures effectively. Additionally, combining theoretical knowledge with hands-on training ensures a better grasp of the procedures. Regular monitoring and review of these control measures also ensure they remain effective as conditions change in the manufacturing environment.
BPRHub supports this effort by providing comprehensive training modules and up-to-date resources on safety and compliance. Reach out to us today to know more.
Modern Risk Assessment Made Easy with BPRHub
Digitized solutions play a crucial role in modernizing risk assessment processes in manufacturing. Platforms like BPRHub leverage automation and real-time monitoring to streamline and enhance the overall efficiency of risk management. Here are some key benefits of implementing such solutions:
- Automation of Compliance Tasks: BPRHub automates various compliance-related tasks, significantly reducing the time and effort required to manage them manually. This automation not only increases efficiency but also minimizes the risk of human error, ensuring that compliance requirements are consistently met.
- Enhanced Risk Management: The platform provides real-time data on potential hazards, allowing organizations to stay ahead of risks as they emerge. By accessing live data, decision-makers can quickly identify and address issues before they escalate, creating a safer work environment.
- Integration with Daily Workflows: BPRHub integrates compliance management seamlessly into daily operations, ensuring that safety protocols and risk assessments are part of the everyday workflow. This integration fosters a culture of safety, as employees are more likely to adhere to compliance measures when they are easily accessible and part of their routine.
- Improved Accuracy and Tracking: Utilizing digitized solutions enhances the accuracy of risk assessments by providing structured data and analytics tools. This reduces the burden of manual documentation and tracking, allowing for better record-keeping and easier access to information when needed.
- Real-Time Reporting and Insights: With BPRHub, organizations can generate real-time reports and insights that inform decision-making and strategy adjustments. This capability enables proactive risk management and enhances overall operational efficiency.
Conducting a thorough risk assessment is vital for maintaining a safe and efficient manufacturing environment. By systematically identifying hazards, evaluating associated risks, and implementing effective control measures, you can significantly minimize incidents and foster a safer, more productive workplace.
FAQ’s
1. What is a risk assessment in manufacturing?
A risk assessment in manufacturing is a systematic process of identifying, evaluating, and mitigating potential hazards that could negatively impact operations, employee safety, or product quality. This proactive approach aims to prevent accidents, ensure compliance.
2. Why is risk assessment important in manufacturing?
Conducting risk assessments is crucial because it:
- Identifies potential hazards before they cause harm.
- Ensures compliance with occupational health and safety regulations.
- Reduces the likelihood of workplace accidents and associated costs.
- Enhances overall operational efficiency by addressing risks proactively.
3. What are the key steps in conducting a risk assessment?
The fundamental steps include:
- Identify Hazards: Examine the workplace to pinpoint potential sources of harm.
- Assess Risks: Evaluate the likelihood and severity of harm from identified hazards.
- Implement Controls: Develop measures to eliminate or reduce risks.
- Monitor and Review: Regularly check the effectiveness of control measures and update them as necessary.
4. Who should be involved in the risk assessment process?
A comprehensive risk assessment should involve:
- Management: To provide support and resources.
- Safety Officers: To offer expertise in hazard identification and control.
- Employees: To provide insights into daily operations and potential risks.
- Maintenance Staff: To identify equipment-related hazards.
5. How often should risk assessments be conducted?
Risk assessments should be performed:
- Regularly, such as annually or biannually.
- Whenever there are significant changes in processes, equipment, or personnel.
- After an incident or near-miss to prevent recurrence.
6. What are common hazards identified in manufacturing?
Typical hazards include:
- Mechanical Hazards: Moving machinery parts that can cause injury.
- Chemical Hazards: Exposure to harmful substances.
- Ergonomic Hazards: Repetitive motions or improper lifting techniques.
- Physical Hazards: Noise, vibration, or extreme temperatures.
- Electrical Hazards: Faulty wiring or equipment.
7. What are control measures in risk assessment?
Control measures are actions implemented to eliminate or reduce risks, including:
- Engineering Controls: Modifying equipment or processes to reduce hazards.
- Administrative Controls: Implementing policies or training to promote safe practices.
- Personal Protective Equipment (PPE): Providing gear like gloves, helmets, or goggles.
8. How is the effectiveness of control measures evaluated?
Effectiveness is assessed by:
- Monitoring incident and near-miss reports.
- Conducting regular safety audits and inspections.
- Gathering feedback from employees on safety practices.
- Reviewing compliance with safety procedures and regulations.
9. What role does employee training play in risk assessment?
Employee training is vital as it:
- Educates staff on potential hazards and safe practices.
- Empowers employees to identify and report risks.
- Ensures proper use of equipment and PPE.
- Promotes a culture of safety within the organization.
10. How can technology assist in conducting risk assessments?
Technology aids risk assessments by:
- Providing digital tools for hazard identification and documentation.
- Facilitating real-time monitoring of equipment and environmental conditions.
- Offering platforms for training and information dissemination.
- Enabling data analysis to identify trends and areas for improvement.
Implementing thorough risk assessments in manufacturing is essential for safeguarding employees, ensuring compliance, and maintaining efficient operations.