Given the growing importance of meeting different standards, maintaining high standards and ensuring compliance is non-negotiable for manufacturers. However, managing complex processes manually can drain resources and multiply errors, leading to inefficiencies that cost both time and money.
Studies show that automating processes can reduce human error in manufacturing by up to 30%. So, the smarter approach is to use quality management system software that automates, streamlines, and centralizes the processes involved in managing quality across an organization.
In this blog, we’ll explore the benefits of using QMS software and how industries like manufacturing, aerospace, food and beverage, and pharmaceuticals stand to gain the most from adopting this powerful tool.
What is a Quality Management System?
A Quality Management System (QMS) can be defined as a framework attuned to several standards, such as ISO 9001, ISO 13485, etc., to provide a blueprint of policies, processes, and procedures that ensure an organization consistently meets or exceeds customer and regulatory requirements. It helps streamline operations, improve efficiency, and maintain a high standard of product or service quality.
ISO 9001:2015 is the leading international standard that outlines the requirements for quality management systems (QMS). While some might refer to a QMS as simply the ISO 9001 standard or the documents associated with it, a QMS is much more than that. Let’s explore their main components.
What Are the Key Components of QMS?
A QMS is centered on continuous improvement by integrating various elements like document control, corrective actions, and performance analysis; hence, they have four major components:
- Quality Control Planning: This involves setting clear objectives and defining the processes and resources required to meet quality standards. While planning, you should consider stakeholder expectations, company success metrics, legal requirements, role assignments, and evaluation frequency to assess and continuously improve processes throughout the quality management cycle.
- Quality Control: Quality control is the process of monitoring and inspecting products or services during production to detect any defects or inconsistencies. This step ensures that the final output meets the predetermined quality standards, using methods such as testing, inspections, and performance evaluations to maintain consistency.
- Quality Assurance: Quality assurance focuses on preventing defects by reviewing processes. It ensures that service delivery is carefully managed at each stage of production and that staff follow best practices to minimize errors and maintain high-quality outcomes.
- Quality Improvement: Quality improvement involves ongoing efforts to enhance processes, products, and services. Through regular analysis, feedback, and corrective actions, organizations can identify opportunities to reduce waste, increase efficiency, and elevate overall quality performance.
What is Quality Management System Software?
Quality management system software (QMS) is a digital solution designed to effectively implement the quality management system without fail by automating and streamlining the management processes across an organization. QMS software provides a centralized platform integrating essential functions such as document control, audit management, corrective actions, and performance analysis to track and enhance quality processes in real-time.
One might wonder why switching to QMS software is necessary; after all, QMS can be implemented manually, and QMS itself ensures improved efficiency. The simple answer is automating tasks to reduce human error, but we’ll elaborate on it.
The Drawback of Manually Processing QMS
- Manual processes could be faster. It requires more time for data entry, tracking, and reporting.
- They are much more prone to human error, which can cause many inefficiencies that drive up costs due to wasted time and resources.
- It does not offer real-time insights, which delays decisions and improvements.
- Managing documents manually makes it harder to track versions, revisions, and approvals.
- Maintaining compliance with industry standards is more difficult without automated tracking and audit trails.
The limitations of manual quality management processes can severely affect an organization’s ability to maintain consistency. Many industries are turning to automated solutions to overcome these challenges.
Manual quality management processes can lead to costly delays, frequent errors, and missed opportunities for real-time improvements. BPRHub offers a solution to these challenges, providing automated tracking, version control, and a dedicated document hub for easy access to real-time data insights and compliance records.
How Quality Management Software Transforms Industries
Quality Management Software (QMS) is transforming industries with high standards and regulatory needs. From manufacturing to healthcare, QMS boosts efficiency, ensures quality, and reduces compliance risks, offering a valuable edge across sectors.
1.Manufacturing
Manufacturing industries rely heavily on precision, consistency, and compliance with safety regulations. QMS software helps streamline production processes, ensuring that quality standards are met at every stage.
It can significantly improve the quality and consistency within the supply chain by providing early visibility into potential issues before they escalate. This proactive approach helps reduce costs, avoid disruptions, and boost customer satisfaction.
As efficiently and maintaining compliance is critical for manufacturing operations, the Audit Hub powered by BPRHub is a centralized audit management system that simplifies the scheduling, tracking, and execution of audits and manages all types of audits necessary for manufacturing. Click here to get a free consultation and start your auditing process.
2.Government
Many government entities often need help with efficient processes for managing policies, procedures, and critical documents. A QMS eliminates these inefficiencies by providing a secure, centralized, browser-based platform for document collaboration, storage, and retrieval.
Government agencies greatly benefit from QMS software by ensuring compliance with various regulatory requirements while enhancing transparency and efficiency.
3.Packaging
In the packaging industry, maintaining consistency is crucial to ensuring products are packed safely and efficiently for transport and sale.
With a QMS in place, packaging companies can avoid challenges such as errors, rework, inconsistent processes across departments, and costly production delays.
QMS software also helps manage supplier relationships more effectively and ensures proper documentation of production processes. This includes organizing and maintaining important documents like Bills of Materials (BOMs), production logs, and revisions, which are critical for smooth and consistent packaging operations.
With QMS software, companies can focus on delivering high-quality, compliant products while minimizing delays and maximizing productivity.
4.Food and Beverage
QMS provides better control over critical business processes, ensuring consistency and adherence to quality standards. It also ensures that the company follows best practices to meet industry quality and compliance requirements.
Effective QMS software helps food and beverage companies establish standardized processes. It makes it easier to track, monitor, and analyze ongoing operations and their outcomes, ensuring continuous improvement and consistency throughout.
It helps companies track compliance with food safety regulations, monitor production processes, and ensure that products consistently meet the highest standards, safeguarding both the business and consumers.
5.Aerospace and Automotive
A major advantage of QMS software process automation is that it reduces human error, saves time, and minimizes costs by streamlining workflows and ensuring compliance with stringent regulations like ISO and AS standards.
QMS software, with real-time monitoring and automation, helps detect and prevent significant failures in complex systems.
The aerospace and automotive industries face stringent safety and quality standards, and QMS software ensures compliance by tracking performance data, enhancing production processes, and reducing risks.
This ultimately boosts the reliability of complex systems and fosters stronger customer relationships.
6.Medical Device
QMS software helps manage regulatory compliance, track product quality, and ensure proper documentation, making it easier to bring safe and reliable devices to market.
By integrating with other business systems such as ERP and LIMS, QMS software ensures seamless collaboration between departments and suppliers, guaranteeing compliance throughout the product lifecycle.
Key features, such as audit management, validation management, and electronic signature capabilities, support adherence to regulatory standards like FDA 21 CFR Part 11 and EU Annex 11. These features not only enhance product quality but also safeguard public health by maintaining strict compliance at every stage of production.
7.Pharmaceutical
Pharmaceutical companies are supposed to comply with strict regulations for drug safety, testing, and production. However, they also face challenges in maintaining compliance, adhering to FDA regulations, and mitigating quality risks.
QMS software supports these efforts by ensuring compliance with Good Manufacturing Practices (GMP), tracking audits, and maintaining thorough documentation for regulatory approval.
It helps ensure compliance with ISO 9001, FDA regulations, and EU MDR, streamlining the path to regulatory adherence. With advanced quality analytics, QMS software equips you with critical data to make informed, data-driven decisions, safeguard your brand's reputation, and accelerate time-to-market for your products, ultimately enhancing operational efficiency and compliance management.
8.Life Science
The life science industry, which includes biotech and healthcare sectors, requires precise documentation, regulatory compliance, and data tracking.
With advanced documentation features, QMS software helps manage research processes, ensure regulatory adherence, and maintain data integrity, enhancing innovation and safety.
Twelve Benefits of Quality Management System Software
The relevance of QMS software across the globe can be analyzed by the revenue generated by the QMS software industry in the subsequent years. The global QMS software market size and outlook research conducted by Horizon Grand View Research concluded that,
“The global quality management software market generated a revenue of USD 10,180.9 million in 2023 and is expected to reach USD 20,655.9 million by 2030.”
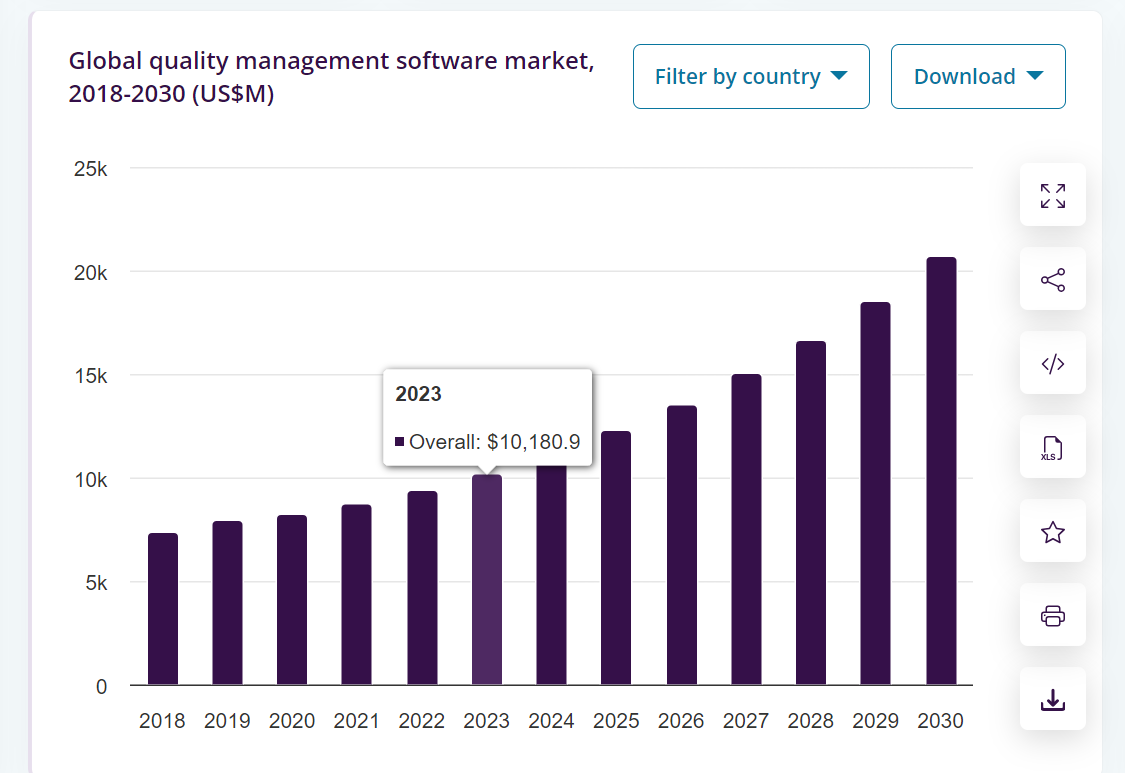
The reason for their exponential growth primarily lies in the benefits that QMS software provides for various industries. From the manufacturing industry to pharmaceuticals, meeting benchmark standards for quality and customer satisfaction is essential, and this can be easily achieved through QMS software. Their benefits are listed below:
1. Management and Integration of Standards
QMS software simplifies the application of regulatory and industry standards across all operations, ensuring compliance is maintained easily. This is done by utilizing some advanced features such as:
- Centralizing documents in a cloud-based cache eliminates the inefficiencies of scattered files and outdated versions, offering quick access to the most up-to-date information.
- Role-based access controls can also be implemented to safeguard sensitive data, ensuring only authorized personnel can view specific documents.
- It makes it easier to adapt to new compliance requirements, allowing organizations to scale into new markets, territories, or sectors seamlessly.
This streamlined approach enables businesses to remain agile in competitive landscapes, focusing on innovation and building relationships rather than creating compliance systems from scratch.
Get a free consultation to discover how BPRHub’s Standard Hub simplifies compliance by integrating multiple domestic and international standards into one centralized, user-friendly platform.
2.Improved Decision Making
QMS software empowers organizations to make informed, data-driven decisions by providing real-time reporting and analytics. With customizable dashboards and metrics, you can monitor key performance indicators, identify trends, and detect potential issues before they escalate.
This allows for proactive decision-making based on accurate, up-to-date information.
The software’s visual data representation helps teams easily review and analyze insights, ensuring that decisions are aligned with best practices and business goals. By adopting this data-driven approach, organizations can enhance both quality and efficiency, meeting ISO standards that emphasize the importance of evidence-based decision-making.
3.Enhances Internal Communication
Quality Management Software (QMS) significantly enhances internal communication by fostering accountability, clarity, and alignment across teams. Here’s how QMS promotes an efficient, cohesive work environment:
- Encourages Accountability and Ownership:
- QMS software clarifies expectations, helping employees understand their roles and responsibilities.
- A centralized platform with an alert system ensures that quality-related information is shared promptly across departments.
- Supports Quality Initiatives:
- QMS aids employee buy-in for quality goals through effective information sharing.
- ISO 9001:2015-aligned QMS clearly defines responsibilities for all levels, ensuring employees recognize their contributions to organizational goals.
- Facilitates Training and Engagement: QMS software assists in employee training and education, keeping everyone informed and engaged in maintaining high standards.
- Enables Senior Management Feedback and Issue Resolution: The platform allows senior leaders to gather feedback, share updates, and address issues efficiently, promoting an environment of open, positive communication.
By streamlining communication and clarifying responsibilities, QMS software cultivates a collaborative work culture that boosts productivity and alignment across the organization.
4.Improved Efficiency and Consistency
Implementing a QMS requires organizations to establish and document best practices across all business functions, from quality control to management reviews. Here’s how QMS supports seamless operations and continuous improvement:
- Establishes SOPs: Developing standard operating procedures (SOPs) and implementing a structured system of checks and balances helps minimize the risk of nonconformance while enhancing overall efficiency within the organization.
- Keeps SOPs Up to Date: QMS software ensures that (SOPs) are kept up-to-date, making audits seamless with centralized checklists and real-time tracking of findings to improve consistency.
- Automates Routine Tasks: By automating routine tasks such as document approval workflows, audit scheduling, and corrective action tracking, QMS software ensures that these processes are carried out smoothly and on time, reducing the risk of human error and non-compliance.
- Optimizes Resource Utilization: This automation not only frees up valuable time for employees to focus on strategic tasks but also ensures consistent process execution every time. By reducing manual efforts and minimizing the potential for errors, QMS software optimizes resource utilization and enhances workflow reliability.
- Enhances Cross-Department Communication: Integrated cross-department communication and precise process documentation further support organizational growth without compromising on quality, leading to sustained efficiency across the business.
5.Efficient Documentation and Record Collection
Manual processes can be time-consuming and prone to errors, leading to missing documents or non-conformities. QMS software automates documentation, organizing records in a structured, easily accessible system. This ensures accurate, up-to-date records are securely stored and readily available when needed.
By streamlining document management, QMS software improves efficiency, allowing organizations to access and manage crucial information quickly and effectively.
6.Reducing Error and Improving Customer Satisfaction
This customer-centric focus of QMS ensures that the entire organization is aligned with meeting customer expectations and building trust and loyalty. Here are the ways by which QMS supports customer loyalty and business growth:
- Aligns the Organization with Customer Expectations: Ensures that products and services consistently meet the highest quality standards. This leads to increased customer loyalty, positive brand reputation, and, ultimately, business growth.
- Facilitates Cross-Department Communication: QMS software connects customer-facing teams with quality assurance managers, streamlining communication between departments like sales, customer service, and production. This integrated approach helps resolve issues quickly and prevent errors from affecting the customer experience.
- Offers Data-Driven Quality Assurance: Allows you to generate reports demonstrating your commitment to quality, which can be used as a powerful marketing tool.
- Increases Long-Term Customer Retention: Customers who receive consistent, high-quality service are more likely to remain loyal, even in the face of competitive offerings, leading to long-term customer retention and increased sales.
7.Efficient Management Review
Management reviews are a key element of ISO standards, requiring top management to evaluate the effectiveness of the QMS regularly. QMS software streamlines this process by the following methods
- Consolidates Essential Data for Reviews: This feature consolidates all essential data and reports into one platform, making it easy to prepare for thorough reviews.
- Generates Detailed Reports: The software generates reports on key performance indicators (KPIs), audit outcomes, non-conformance trends, and more, offering a comprehensive view of quality management efforts.
- Streamlines Change Management: It provides tools to track and implement changes to processes, equipment, or personnel with minimal disruption.
- Automation: Automated notifications and approval workflows keep all stakeholders informed, ensuring smooth transitions.
This leads to a more cohesive approach to both management review and change implementation, ultimately improving overall efficiency.
8.Advanced Risk Assessment
A QMS provides a robust framework for identifying and managing risks related to product quality, safety, and compliance. Here’s how QMS software supports effective risk management through structured, proactive measures:
- Establishes a Framework for Risk Management: With QMS software, organizations can implement standardized processes for risk identification, assessment, and mitigation, ensuring consistency across all departments.
- Detection and Prevention: This proactive approach allows potential risks to be detected early, enabling preventive measures to reduce their likelihood or minimize their impact.
- Streamlines Risk Mitigation: The software streamlines risk mitigation through real-time monitoring, automation alerts, and tools that assign and track action items. Tracking issues to closure and identifying root causes helps prevent recurring problems.
- Enhances Risk Communication: Standardized procedures and documentation also improve risk communication. This ensures all team members understand their roles in managing risks, fosters a shared sense of responsibility, and enhances overall risk management.
9.Minimizing Operational Cost
One of the major advantages of QMS software is its ability to reduce operational costs and company resources and save time by:
- The software helps avoid costly rework, recalls, and defects by minimizing the risk of errors that could impact ISO certification or customer satisfaction.
- The automation of most tasks and the optimization of workflows allow organizations to achieve more without the need for additional staff, directly contributing to operational savings and improving the company's bottom line.
- Streamlining document management reduces costs associated with manual systems, saves time, and enables organizations to reallocate resources toward more strategic, high-value initiatives.
10.Enhancing Product Quality
The primary benefit of QMS software lies in its ability to enhance product quality. By providing tools for continuous monitoring and analysis, the software helps identify potential quality issues early, allowing for quick corrective actions.
This proactive approach ensures that products consistently meet quality standards before they reach customers.
It also streamlines audit inspections, improving the overall quality of products before they are dispatched, further reinforcing the reliability and consistency of the output.
11.Trading Across Border
Internationally expanding a business requires strict adherence to global regulations and quality standards, and QMS software plays a pivotal role in making this process smoother.
With a system that ensures compliance with international standards, such as ISO 9001, companies can not only achieve certification more quickly but also maintain ongoing compliance across borders.
Ultimately, QMS software enhances global customer satisfaction, supporting business growth and success in international markets.
12.Making it Easy for Continuous Improvement
Continuous improvement is a core principle of QMS that extends well beyond the initial certification, driving ongoing optimization throughout the organization. QMS software supports this by integrating the Plan-Do-Check-Act (PDCA) cycle, encouraging every employee to contribute equally to optimization efforts.
Quality management system software collects data on nonconformances and deviations, tracks investigations, and resolves issues in real time.
Alerts and reminders ensure timely reporting, investigation, and resolution of these issues, addressing root causes and implementing preventive actions. This systematic approach not only prevents recurring problems but also promotes ongoing improvement across the organization.
BPRHub: A Trusted QMS Solution Across Industries
From manufacturing and aerospace to pharmaceuticals and life sciences industries, QMS software enhances efficiency, improves product quality, and fosters continuous improvement by automating critical processes, providing real-time insights, and ensuring adherence to regulatory requirements.
With so many options available in the market, finding quality management software that ticks all the boxes can be difficult. However, one software that can be used across any industry and has advanced features that integrate multiple standards is BPRHub.
BPRHub is cloud-based quality management software designed to simplify complex compliance processes and help organizations meet regulatory requirements by automating compliance processes, streamlining workflows, and enabling data-driven decision-making.
It also Integrates smoothly with Asset Hub, Risk Hub, Master Product, and Production Hub for simplified evidence collection and management.
QMS software ensures that businesses stay agile; hence, it is crucial to choose a QMS software that provides alerts for the changing compliance landscape, a platform for multiple standard integrations, and a streamlining of the compliance process.
With advanced features and seamless integrations, BPRHub can transform your compliance processes, streamline workflows, and effortlessly manage your quality.
FAQ’s
1. What is Quality Management System (QMS) software, and how does it work?
Ans: QMS software is a digital solution that automates and streamlines quality management processes. It centralizes essential functions like document control, audits, and performance tracking, helping organizations enhance efficiency, ensure compliance, and maintain consistent quality standards.
2. How can QMS software improve efficiency in manufacturing?
Ans: QMS software reduces human error, automates routine tasks, and streamlines workflows. It provides real-time insights, enabling proactive decision-making and improving consistency across production processes, ultimately saving time and resources in manufacturing operations.
3. How does BPRHub simplify quality management across industries?
Ans: BPRHub is cloud-based QMS software that automates compliance processes, integrates multiple standards, and provides real-time insights. Advanced features like centralized document management and seamless integrations effortlessly help organizations enhance quality and ensure compliance.