As a manufacturing leader, you're no stranger to the challenges of maintaining top-notch quality while juggling complex operations, tight regulations, and evolving customer demands. It's a delicate balance that can make or break your business. But what if I told you there's a proven framework that can help you navigate these obstacles and unlock a new level of excellence?
Welcome to the transformative world of quality management system (QMS) principles.
In a landscape shaped by Industry 4.0 and the rising role of data analytics in quality control, manufacturing leaders are leveraging innovative technologies to stay ahead. For example, augmented and virtual reality are used in operator training, reducing errors and enhancing product quality.
In this in-depth guide, we'll explore the quality management system principles that can revolutionize your manufacturing operations. Get ready to boost efficiency, reduce risks, and delight your customers like never before.
These principles are based on ISO 9001, the international standard for quality management systems, designed to help businesses deliver consistent quality and build trust.
1. Customer Focus: The Heart of Quality
By adopting quality management system principles like customer focus, you can ensure your products meet and exceed expectations. This is the beating heart of any successful QMS because, at the end of the day, your business exists to serve your customers. By keeping them at the center of your decisions and processes, you can ensure you're truly delivering the value they expect.
So, what does customer focus really mean in practice? It's all about:
- Deeply understanding your customers' unique needs, preferences, and pain points - Gain valuable insights into what matters most to them, tailoring your approach to meet their needs and expectations.
- Building long-term loyalty and satisfaction through consistent, high-quality experiences - Foster customer loyalty by delivering reliable, high-quality experiences that keep them coming back.
- Regularly gathering and acting on customer feedback to drive continuous improvement - Collect feedback frequently and use it to refine your offerings, ensuring your quality evolves with customer expectations.
When you make customer centricity a top priority, you'll not only retain your existing clients but also attract new ones who appreciate your unwavering commitment to quality.
By implementing a zero-defect manufacturing approach, companies like Ford and Boeing ensure they meet customer expectations for flawless quality. This proactive control over quality helps manufacturers build long-term customer loyalty.
Ready to put your customers first? Discover how BPRHub's platform can help you enhance your customer focus through our quality management solutions.
2. Visionary Leadership: Setting the Tone for Success
Effective quality management system principles start with leadership that values quality, setting the tone for success. Great quality doesn't happen by accident - it requires strong, visionary leadership to set the tone and rally the entire organization around a shared purpose.
This principle emphasizes the critical role leaders play in cultivating a culture of quality and excellence.
As a leader, your responsibilities include:
- Establishing a clear, unified vision and direction for your quality management initiatives - Create a shared vision that aligns everyone with quality objectives, ensuring clarity and commitment across the organization.
- Building a supportive, collaborative work environment that empowers your team - Foster an environment where teamwork and open communication empower everyone to contribute meaningfully to quality goals.
- Leading by example and actively participating in the achievement of quality goals - Demonstrate your commitment to quality by setting a strong example and engaging directly in the pursuit of quality excellence.
With developing economies contributing significantly to global trade, visionary leadership in manufacturing must embrace quality management practices to compete effectively.
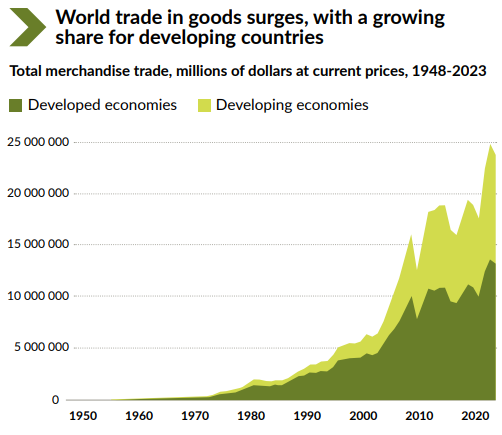
The growth highlighted in the graph points to the need for leaders who prioritize quality to build trust and expand into international markets.
When your leadership team is fully invested in quality, it sends a powerful message throughout your organization. Your employees will feel inspired to contribute their best, and your customers will notice the difference in your products and services. Strong leadership is essential to navigate regulatory landscapes that are increasingly aligned with global standards.
In 2024, the FDA updated its Quality System Regulation to harmonize with ISO 13485:2016, reflecting the industry's global alignment. Set a strong leadership foundation for quality management. Get insights on building a supportive, collaborative environment with BPRHub. Contact us today.
3. Engaged and Empowered Employees: Your Quality Champions
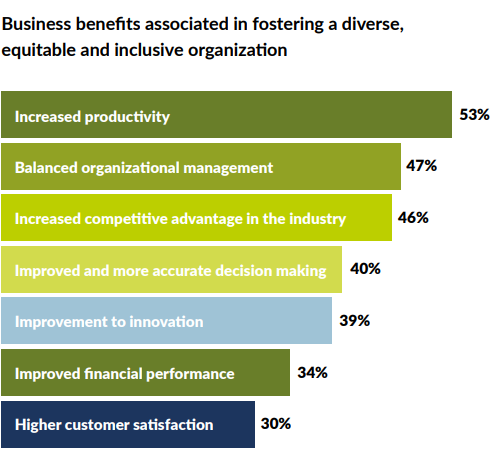
Speaking of your team, the third principle of QMS highlights the importance of actively engaging and empowering your people. After all, they're the ones who bring your quality management system to life every day. Engaging and empowering a diverse workforce is essential for quality excellence.
As shown in the chart, fostering diversity, equity, and inclusion (DEI) brings numerous business benefits, from increased productivity to improved decision-making and innovation. By building a DEI-focused culture, organizations can enhance their QMS efforts, creating a more collaborative and quality-driven work environment.
By tapping into the skills, ideas, and passion of your employees, you can:
- Motivate and enable your team to take ownership of quality objectives - Empower your team to take responsibility for quality goals, encouraging active involvement and commitment to excellence.
- Foster a collaborative, creative environment where everyone contributes to improvement - Cultivate a collaborative and innovative atmosphere where each team member feels valued and motivated to contribute to continuous improvement.
- Build a quality-focused culture where excellence is the norm, not the exception - Establish a culture where quality is central, ensuring that high standards are consistently met and embraced by all.
When your people feel invested in the success of your QMS, they'll go above and beyond to deliver outstanding results. It's a win-win for your business and your customers.
4. Process-Driven Efficiency: The Backbone of Quality
Now, let's dive into the technical side of quality management. The process approach principle emphasizes the importance of viewing your business activities as interconnected processes, rather than a series of isolated tasks. Implementing quality management system principles focused on efficient processes can minimize waste and streamline operations.
By managing your operations this way, you can:
- Optimize efficiency and eliminate bottlenecks by understanding process interdependencies - Identify and manage the links between processes to boost efficiency and remove bottlenecks, creating smoother workflows.
- Leverage digital tools and platforms to streamline and automate your workflows - Use digital solutions to simplify and automate workflows, reducing manual effort and increasing productivity.
- Continuously analyze and refine your processes to enhance performance - Regularly review and adjust processes to improve performance, ensuring your operations stay efficient and effective.
A process-focused mindset allows you to identify areas for improvement, minimize waste, and ensure your quality management system runs like a well-oiled machine. A process-driven approach to quality management becomes more effective when supported by data-driven insights. The rise of Industry 4.0 technologies allows manufacturers to identify inefficiencies proactively and streamline operations.
Optimize your processes from start to finish with BPRHub's seamless system integration. Streamline Your Processes Today. Book a demo.
5. Continuous Improvement: The Engine of Innovation
Continuous improvement is increasingly tech-driven, with new trends reshaping quality management practices. As shown in the chart below, immersive technologies, IoT, and computer vision are some of the leading advancements helping manufacturers improve quality control, efficiency, and accuracy.
Embracing these trends allows for an agile, innovation-driven approach to quality.
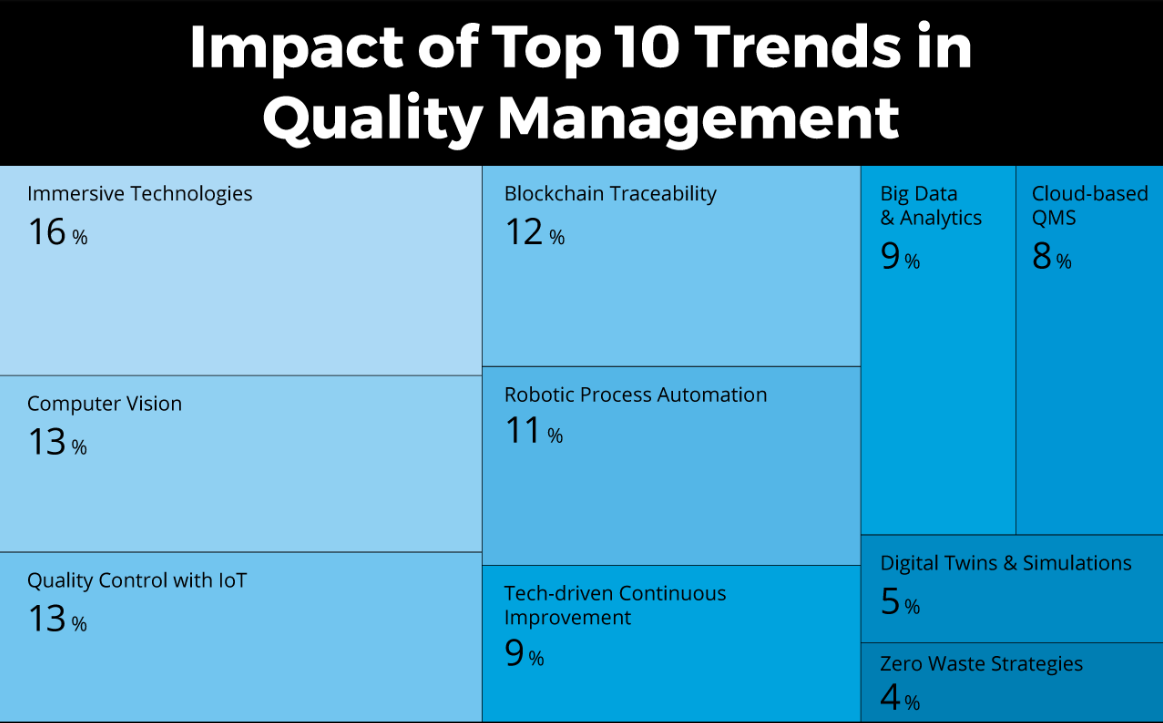
No matter how well-oiled your processes may be, there's always room for enhancement. The improvement principle is all about fostering a culture of ongoing betterment, where you're constantly seeking ways to elevate your products, services, and operations.
This could involve:
- Learning from past experiences and driving innovative solutions - Reflect on past experiences to fuel innovation, using lessons learned to develop forward-thinking solutions.
- Utilizing customer feedback to identify opportunities for improvement - Gather and analyze customer feedback to uncover valuable insights, guiding improvements that meet evolving needs.
- Implementing a structured approach to continually enhance your quality management system - Adopt a systematic approach to refine your QMS, ensuring continuous quality improvement and alignment with best practices.
The 2024 World Manufacturing Report highlights the need for strategic foresight in manufacturing to stay agile amid geopolitical, economic, and technological shifts. By embracing a mindset of continuous improvement, you'll stay ahead of the curve, anticipate your customers' evolving needs, and solidify your reputation as a quality leader in your industry.
6. Data-Driven Decisions: The Path to Informed Excellence
In today's data-driven landscape, evidence-based decision-making is essential for achieving true quality excellence. This principle emphasizes the importance of basing your choices on objective data and thorough analysis, rather than gut instinct or assumptions.
When you adopt a data-driven approach, you can:
- Improve the accuracy and effectiveness of your strategic decisions - Use precise data to enhance strategic decisions, ensuring each choice aligns with business goals and drives impactful results.
- Leverage analytics to identify areas for improvement and track progress - Harness analytics to pinpoint improvement areas and monitor progress, keeping your business on a path of continuous growth.
- Make confident, informed choices that drive tangible results for your business - Empower your decisions with data insights, making impactful choices that lead to measurable success.
By grounding your quality management system in facts and evidence, you'll be able to navigate challenges, capitalize on opportunities, and consistently deliver the highest level of value to your customers.
7. Collaborative Partnerships: Unlocking New Possibilities
The final quality management principle for a successfull QMS is all about relationship management - specifically, cultivating strong, mutually beneficial partnerships with your key stakeholders, including customers, suppliers, and industry peers.
When you prioritize these collaborative relationships, you can:
- Align goals, share resources, and manage risks across your value chain
Coordinate objectives, optimize resource allocation, and proactively manage risks throughout your value chain to build a unified and resilient operation.
- Leverage the expertise and insights of your network to drive innovation
Tap into your network’s knowledge and experience to fuel innovation, using shared insights to address challenges and create valuable solutions together.
- Unlock new opportunities for growth and improvement that you couldn't achieve alone
Collaborate with partners to access growth opportunities and drive improvements that would be difficult to accomplish independently, fostering mutual success.
Embracing these seven quality management system principles can elevate your manufacturing standards and drive your organization forward. By fostering a spirit of collaboration and trust, you'll build a solid foundation for long-term success, resilience, and quality excellence.
Unlock Your Manufacturing Superpowers with BPRHub
Alright, let's recap - we just dove deep into the 7 essential principles that can revolutionize your manufacturing operations and propel your business to new heights of success. Pretty exciting stuff, right? Now, I know what you might be thinking - "That all sounds great, but how do I actually put these principles into practice?"
That's where the team at BPRHub comes in.
As a leading provider of comprehensive compliance management solutions, BPRHub is uniquely positioned to help you effortlessly implement these quality management principles and take your manufacturing game to the next level. Here's how:
✅ Laser-Focused Customer Focus: BPRHub's intuitive platform puts your customers' needs front and center, helping you consistently deliver the high-quality experiences they crave.
✅ Visionary Leadership Tools: Our advanced analytics and reporting capabilities empower your leadership team to make informed, strategic decisions that drive quality excellence.
✅ Engaged Employees, Elevated Performance: BPRHub's workflow automation and process optimization features free up your team to focus on innovation and continuous improvement.
✅ Streamlined, Connected Processes: Say goodbye to siloed operations - BPRHub integrates your critical systems and data to ensure seamless, end-to-end quality management.
✅ Continuous Improvement, Powered by Data: With real-time insights at your fingertips, you can identify opportunities, iterate on your processes, and stay ahead of the curve.
✅ Collaborative Partnerships, Amplified: BPRHub helps you build stronger relationships with suppliers, regulators, and other key stakeholders to unlock new possibilities.
So, if you're ready to take your manufacturing operations to the next level and leave your competitors in the dust, let's chat. The BPRHub team is standing by to give you a personalized consultation and show you how our cutting-edge platform can help you effortlessly implement these transformative quality management principles.
Don't settle for anything less than excellence - it's time to unlock your manufacturing superpowers and dominate your industry. What are you waiting for? The future of your business is calling!