Did you know that around 30% of workplace conflicts stem from unclear roles and responsibilities? Imagine a world where every team member knows exactly what they're supposed to do, when, and how—no guesswork, no finger-pointing, just pure organizational harmony. Understanding the key elements of an ISO 9001 job description is crucial for ensuring that every team member contributes effectively to the organization’s quality management system.
ISO 9001 is the blueprint that helps businesses create this kind of clarity. It's a comprehensive approach to defining who does what, when, and why. In this blog, we're diving deep into the world of organizational structure through the lens of ISO 9001. We'll break down how defining roles isn't just about job titles, but about creating a workplace where accountability, efficiency, and quality go hand in hand. Ready to transform the way you think about workplace structure? Let's get started.
Empowering Teams Through Defined Responsibilities
Defining roles and responsibilities is a foundation for achieving organizational success. Research shows that organizations with clearly defined roles are 25% more likely to achieve their goals. Here’s how defining roles within your ISO 9001 framework can enhance your Quality Management System (QMS):
1. Documenting Roles and Responsibilities
- Clarity in Expectations: Clear documentation ensures everyone understands what is expected of them, reducing errors and task duplication.
- Compliance Assurance: Helps meet ISO 9001 standards by assigning accountability and aligning processes with regulatory requirements.
- Efficiency in Complex Industries: This is especially critical in highly regulated sectors where compliance impacts operational success.
2. Promoting Employee Understanding
- Role Awareness: Employees must know how their work contributes to the QMS objectives.
- Engagement and Ownership: When roles are clearly communicated, employees are more engaged and take ownership of their responsibilities.
3. Aligning Roles with Organizational Goals
- Strategic Alignment: Ensure every role supports the broader organizational objectives, creating a unified approach toward continuous improvement.
- Streamlined Operations: Well-aligned roles reduce redundancies and improve overall efficiency.
4. Achieving ISO 9001 Certification
- Avoiding Confusion: Clearly outlined roles prevent miscommunication, ensuring everyone contributes effectively to compliance goals.
- Collaborative Effort: When roles and objectives are aligned, certification becomes a collective and seamless achievement.
Defining roles and responsibilities ensures a shared understanding across the organization, driving both compliance and operational success. A clear ISO 9001 job description fosters collaboration and accountability, making certification not just a goal but an integral part of business excellence. Now that we’ve seen the importance of defining roles, let’s take a deeper dive into how you can effectively develop your organizational structure and job descriptions to align with ISO 9001 standards.
Building Organizational Structure with Clear Job Roles
Creating a solid organizational structure that reflects QMS roles is essential for the smooth operation of ISO 9001 processes. By clearly establishing job roles within your ISO 9001 framework, your company can expect operational improvements. ISO-certified organizations report an average 15% increase in operational efficiency and a 10% improvement in customer satisfaction. This includes developing clear job descriptions, defining decision-making authorities, and ensuring that all personnel know their specific tasks and responsibilities.
1. Creating an Organizational Chart that Reflects QMS Roles:
An organizational chart is a visual representation of the structure of roles and responsibilities within your company. This chart should be updated regularly to reflect changes in roles, responsibilities, and reporting lines as your QMS evolves. A clear organizational chart helps ensure that each person’s role within the QMS is well understood, aiding both management and employees in navigating their daily tasks.
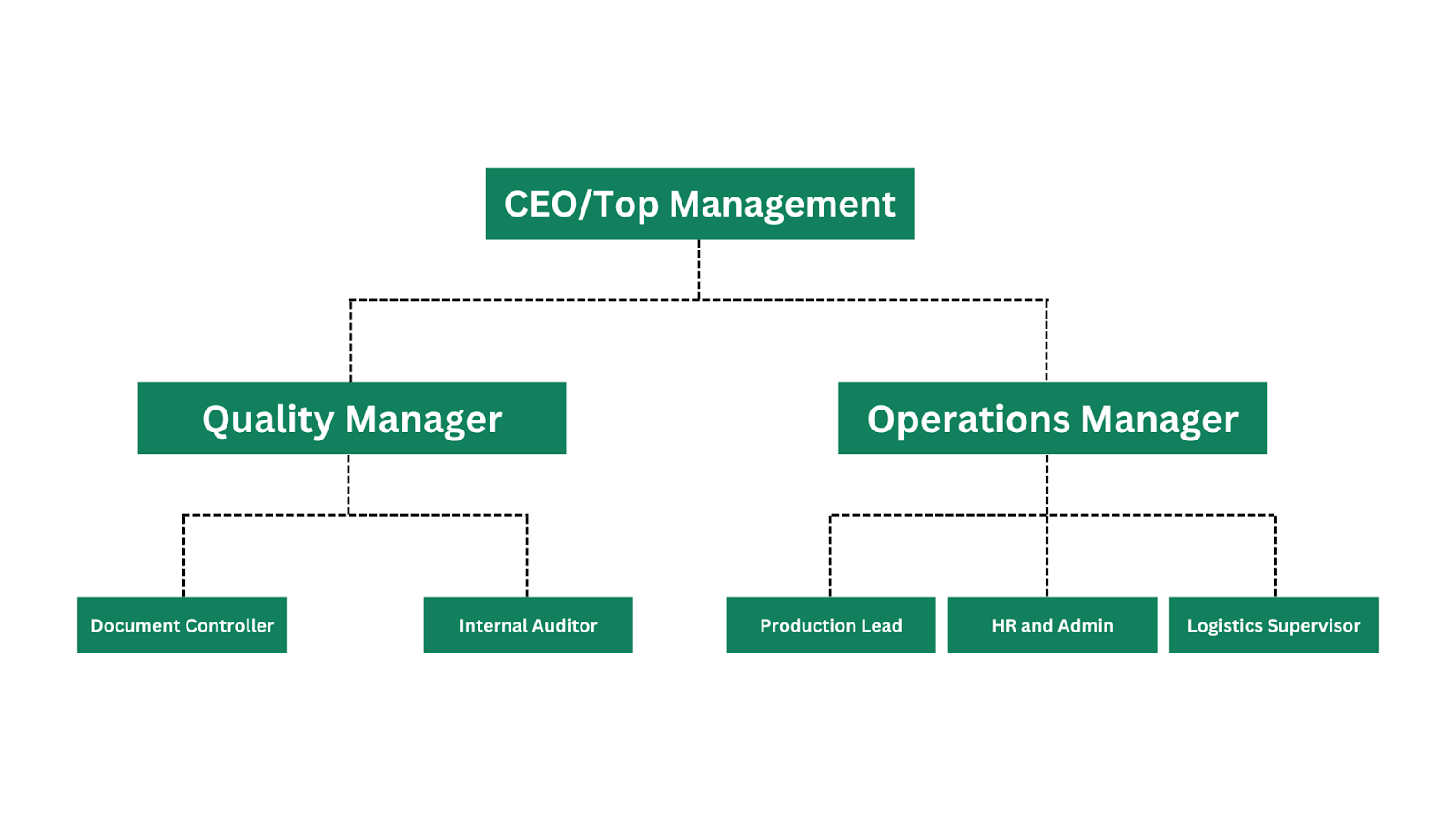
For example, This QMS organizational chart shown above outlines key roles and reporting lines:
- CEO/Top Management: Oversees QMS alignment with business goals.
- Quality Manager: Ensures compliance and quality assurance.
- Operations Manager: Aligns operations with QMS standards.
- Supporting Roles: Document Controller, Internal Auditor, Production Lead, HR/Admin, and Logistics Supervisor manage specific responsibilities like audits, documentation, training, and supply chain quality.
2. Establishing Job Descriptions with Specific Responsibilities and Authorities:
Job descriptions should include specific responsibilities, decision-making authorities, and required qualifications. This helps define what is expected from each role and ensures that employees are prepared for their responsibilities. For instance, a Quality Manager should have clear responsibilities for maintaining quality standards, while a Production Manager’s duties might focus on improving efficiency.
Example Chart: Job Descriptions
3. Importance of Documenting Job Titles, Tasks, and Required Qualifications:
Documenting job titles, tasks, and qualifications ensures clarity and alignment within the organization. It helps recruit the right talent, evaluate performance, and design targeted training programs. Clear qualifications for each role ensure employees have the necessary skills and expertise to meet job expectations. For instance:
- Quality Manager: ISO 9001 experience and knowledge of compliance standards.
- Production Manager: Engineering background and production planning expertise.
- Internal Auditor: Certified in ISO 9001 auditing.
- Document Controller: Proficiency in document management and QMS practices.
As the organization grows, this documentation becomes a vital reference for scalability and operational consistency. When developing your organizational structure, creating detailed ISO 9001 job descriptions for each role is essential to ensure alignment with the quality management system's objectives. When your organization aligns job roles with your QMS, you’re building the foundation for continuous improvement and ISO 9001 compliance.
Building Clarity: Communicating Roles Across the Organization
Clear communication is key to ISO 9001 compliance. In fact, organizations with effective inter-departmental communication reduce compliance issues by up to 40%. Miscommunication can lead to compliance failures and inefficiencies, so it’s essential to have clear methods for disseminating information about job roles and responsibilities.
Clear Communication of Roles
Use training sessions, team meetings, and accessible documentation to communicate defined roles and responsibilities effectively. Ensure all employees understand how their roles align with the organization’s goals.
Effective Communication Methods:
- Regular training sessions and workshops should be conducted to reinforce understanding of QMS roles.
- Use visual aids like organizational charts and job descriptions to provide clarity.
- Leverage digital platforms like intranets for ongoing discussions and easy access to role-related updates.
Connecting Roles to Customer Requirements
- Highlight how each role impacts the end customer, ensuring everyone understands their contribution to maintaining high-quality standards.
- Encourage teams to focus on fulfilling customer needs, from production quality to customer feedback management.
Continuous Reinforcement: Schedule periodic reviews to reassess and re-communicate roles, ensuring alignment with evolving QMS and organizational objectives.
To maintain an effective QMS, it’s essential that your team clearly understands the ISO 9001 job description for their position, which helps foster a culture of accountability. This promotes a collaborative environment where everyone is engaged in the pursuit of quality and continuous improvement.
Is your team communicating their roles effectively? If not, BPRHub’s Compliance Hub can help you improve communication and keep your team aligned. Reach out to us at hello@bprhub.com for tailored solutions.
As your organization begins to communicate roles effectively, it’s important to remember that the leadership team plays a crucial role in ensuring compliance and guiding improvement efforts. Let’s look at management's role in QMS.
The Impact of Leadership on QMS Performance
Top management plays a critical role in the success of a QMS. Top management should ensure that each ISO 9001 job description aligns with the overall quality strategy and provides employees with clear expectations of their role in compliance. They are responsible for driving the implementation, monitoring performance, and ensuring continuous improvement. Their involvement is crucial to aligning the entire organization with ISO 9001 objectives.
- Assigning Relevant Roles During Organizational Changes: As organizations grow or change, management must reassess and clearly define roles in line with ISO 9001 requirements. Introducing new departments or production lines requires proper role allocation to maintain accountability and compliance.
- Preserving Integrity and Seeking Opportunities for Improvement: Regular process reviews are essential to uphold QMS integrity. Management can use audits, data analysis, and cross-functional teams to identify inefficiencies and optimize operations, ensuring continuous improvement.
- Top Management's Involvement in QMS Performance Review and Decision Making: Top management ensures QMS effectiveness through regular performance reviews. These reviews help evaluate compliance, identify gaps, and drive strategic decisions, keeping the organization competitive and aligned with regulations.
Management involvement is critical for sustaining your ISO 9001 certification. Companies with active leadership in their QMS are 40% more likely to maintain certification and see ongoing improvements. Management’s involvement in defining roles and reviewing QMS performance is essential to maintain ISO 9001 certification and drive continuous improvement. Their commitment ensures that roles are aligned with organizational objectives and that everyone in the company is working toward a common goal.
Is your management team fully equipped to oversee QMS compliance? BPRHub’s Audit Hub allows for real-time audits and reviews, helping leadership stay on top of compliance. Book a demo here to see how we can support your management team.
The next key role in ensuring ISO 9001 compliance is the Quality Management Representative (QMR). Let’s explore how this position drives success within your QMS.
How the QMR Drives Quality and Compliance
The Quality Management Representative (QMR) plays a pivotal role in ensuring the QMS is running smoothly and meeting ISO 9001 standards. In fact, 92% of organizations with a designated QMR report more efficient audits and better compliance tracking. Acting as the liaison between management and the rest of the organization, the QMR oversees the effectiveness of quality management processes.
- Leadership and Direction: Guides in implementing and maintaining the QMS, ensuring all employees are trained in their roles and responsibilities with the resources needed for success.
- Liaison for Feedback: Acts as a bridge between staff and top management, conveying feedback on QMS effectiveness to support informed decisions on improvements and training.
- Coordination of Processes: Oversees QMS processes, ensuring compliance with ISO 9001 standards. Manages training initiatives and document control systems to uphold quality and regulatory requirements.
The QMR is an integral part of the ISO 9001 compliance process. By coordinating QMS processes and ensuring communication between management and employees, the QMR helps maintain the system’s effectiveness and drives continuous improvement.
Does your organization have a dedicated QMR? If not, BPRHub’s Compliance Hub can help you define and manage this crucial role within your organization. Request a demo to get started!
With the role of your QMR in place, the final step is ensuring that your QMS is constantly evolving. Let’s look at how to implement and maintain a robust QMS that ensures ongoing compliance and improvement.
Maintaining QMS Excellence for Long-Term Success
Real-world applications of ISO 9001 demonstrate its value. A report by Quality Digest found that 70% of companies saw a significant boost in customer loyalty and retention after implementing ISO 9001. ISO 9001 compliance doesn’t stop once the system is in place—it requires ongoing maintenance and monitoring to ensure continued success.
Defining, Deploying, and Maintaining QMS Processes
Creating and maintaining clear, well-documented processes is the cornerstone of ISO 9001 compliance. Here’s how to ensure success:
- Define Clear Processes: Outline every step of key operations to ensure consistency and alignment with ISO 9001 standards.
- Deploy Effectively: Provide training and resources to ensure all employees understand and can follow the defined processes.
- Identify Improvement Opportunities: Use audits and reviews to pinpoint bottlenecks, redundancies, or inefficiencies in current workflows.
A well-maintained QMS not only ensures compliance but also fosters operational excellence.
Monitoring Compliance Through Internal Audits
Internal audits are the backbone of QMS monitoring. Their role goes beyond compliance checks to include:
- Verification of Compliance: Ensure that processes are being followed and that desired outcomes are achieved.
- Early Issue Detection: Catch potential compliance problems early to prevent them from escalating.
- Actionable Insights: Use audit findings to drive meaningful improvements across the organization.
Regular internal audits provide valuable feedback, keeping your QMS aligned with business and regulatory goals.
Facilitating Management Reviews and Suggesting Improvements
Management reviews play a critical role in maintaining and enhancing ISO 9001 compliance. Key focus areas include:
- QMS Performance Assessment: Evaluate how well the system supports organizational goals and regulatory requirements.
- Feedback for Improvement: Discuss audit results, compliance challenges, and areas needing adjustments.
- Continuous Improvement: Embrace a proactive mindset to ensure the QMS evolves alongside organizational needs and market demands.
By involving management in regular reviews, you ensure top-down support for maintaining an effective and future-ready QMS. ISO 9001 compliance is an ongoing process. Regularly defining and refining QMS processes, conducting internal audits, and holding management reviews are essential for sustained compliance. A focus on continuous improvement helps keep your QMS effective and aligned with your business goals. With tools like BPRHub, you can streamline these processes for greater efficiency and long-term success.
Aligning Your Organization for Success
ISO 9001 compliance is an ongoing journey that requires clear role definitions, effective communication, and management involvement at all levels of your organization. By defining roles, creating detailed job descriptions, and ensuring everyone understands their responsibilities, you not only improve compliance but also enhance overall efficiency.
At BPRHub, we understand the challenges manufacturers face in maintaining ISO 9001 compliance. Our cloud-based compliance management platform helps automate processes, streamline workflows, and provide real-time insights into your manufacturing operations. With BPRHub, you can ensure that your QMS is always up-to-date and functioning at its best. If you're unsure whether your ISO 9001 job descriptions are clear and effective, BPRHub’s tools can help you streamline the process and ensure compliance across your organization.
Want to learn more about how BPRHub can support your ISO 9001 journey? We can help you streamline your compliance processes, automate audits, and improve documentation. Visit our website to learn more, or contact us at hello@bprhub.com to schedule a personalized demo.
FAQ’s
1. What are the key roles in an ISO 9001-compliant organization?
Key roles in an ISO 9001-compliant organization include the Quality Manager, who oversees the QMS, Internal Auditors responsible for conducting audits, Process Owners who manage specific processes, and Top Management, which leads the strategic direction and continuous improvement of the QMS.
2. Why is it important to define roles and responsibilities in ISO 9001?
Defining roles is crucial for ensuring accountability, reducing confusion, and meeting compliance requirements. Clear responsibilities make it easier to achieve organizational objectives and maintain consistent quality.
3. How do job descriptions fit into ISO 9001 compliance?
Job descriptions help define the specific duties and authorities related to ISO 9001 compliance. They ensure that each employee understands their role in the QMS and how they contribute to maintaining quality standards.
4. What happens if roles and responsibilities are not clearly defined?
If roles are unclear, it can lead to confusion, inefficiency, and even non-compliance. This can negatively impact the QMS, causing delays, mistakes, and missed opportunities for improvement.
5. Can BPRHub help with managing ISO 9001 compliance roles?
Yes! BPRHub’s Audit Hub can streamline role definitions and help you maintain compliance. Whether you need to document job descriptions or automate compliance processes, BPRHub offers tools that ensure efficiency and accuracy. Try a demo or contact us at hello@bprhub.com to learn more.
6. How can ISO 9001 roles evolve with organizational changes?
As your organization grows or shifts, it’s important to regularly reassess roles and responsibilities to ensure they remain aligned with your ISO 9001 objectives. This ensures that any changes in the structure or workforce do not disrupt compliance or process efficiency.