Many companies rely on external consultants for audits, often resulting in surface-level judgments and additional costs without true understanding. The audit ends up being just a checkmark, not a learning opportunity. By crafting your own tailored ISO 13485 checklist for internal audit, you gain deeper insights into your operations, uncover hidden gaps, and become more efficient in managing your QMS.
This blog will help you create a well-defined checklist, covering the key components, the benefits, and the steps to create an ideal checklist that ensures compliance and drives continuous improvement.
What is the ISO 13485 Audit Checklist for Internal Audit?
An ISO 13485 audit checklist for internal audit is an essential tool used to ensure that your quality management system (QMS) complies with the standards outlined by ISO 13485. This checklist serves as a comprehensive guide, helping auditors assess processes, identify gaps, and confirm that regulatory requirements are met. For any company working in the medical device industry, an internal audit is an important part of maintaining product quality, regulatory compliance, and improving operational efficiency.
Let’s break down the components of an effective internal audit checklist that will ensure a thorough and successful audit process:
1. Defining Audit Scope and Planning (Clause 8.2.4)
The first step in an internal audit is to define the scope of the audit clearly. This involves determining the areas of your QMS that will be examined, the specific departments, and the processes that need to be evaluated. Planning ensures that resources are allocated properly, the audit team knows what to focus on, and you can schedule the audit without disrupting daily operations. When you define the audit scope, consider the following:
- The scope of your QMS processes.
- The objectives of your internal audit.
- Includes the things that need to be covered and the ways to assess each area (documents, interviews, and observations).
2. Involving Management Responsibilities and Reviews (Clause 5.6)
An ISO 13485 internal audit checklist should emphasize management's role in the quality management system. It’s critical that senior leadership is involved in the audit process, not just for providing resources but also for reviewing the audit findings. Management reviews are a requirement under ISO 13485 to assess the effectiveness of the QMS and take corrective actions when necessary. During the audit, ensure that the following is evaluated:
- Leadership’s involvement in the establishment of QMS policies.
- Review of audit reports by management to determine the effectiveness of the QMS.
- Adequacy of management review procedures.
3. Incorporating Design and Development Processes (Clause 7.3)
Design and development processes are at the heart of producing medical devices that meet regulatory and customer requirements. An effective audit checklist should evaluate whether these processes are well documented, followed, and aligned with the ISO 13485 standards. The audit should focus on:
- The documented design and development procedures.
- Ensuring that design inputs are clearly defined and reviewed.
- Verification and validation activities to confirm that the final product meets intended use and regulatory standards.
- The management of design changes and how they are controlled and communicated.
4. Ensuring Production and Process Controls (Clause 7.5)
The production phase of any medical device is critical, and maintaining process control ensures that products are consistently produced according to specifications. This component of the audit checklist will evaluate whether controls are in place to ensure quality during the production and manufacturing stages. Key areas to review include:
- Manufacturing procedures and whether they are followed correctly.
- Process controls that ensure product quality, including equipment calibration and maintenance.
- Validation and verification of production processes to ensure they meet specified requirements.
- Traceability of each product through production stages.
5. Implementing Corrective and Preventive Actions (CAPA) (Clause 8.5.2)
A critical part of your QMS is the implementation of Corrective and Preventive Actions (CAPA). An effective audit checklist ensures that your company identifies, investigates, and addresses non-conformances, root causes, and potential risks before they result in product defects or non-compliance. During the audit, you’ll want to confirm:
- The process for identifying non-conformances and initiating CAPA.
- Root cause analysis methods.
- Whether CAPA effectiveness is monitored and whether implemented actions prevent the recurrence of issues.
- Review of previous CAPA actions and their outcomes.
6. Managing Purchasing Controls (Clause 7.4)
Purchasing controls ensure that any external suppliers or contractors meet your quality standards and regulatory requirements. Auditing this component is vital to confirm that your purchasing practices align with ISO 13485. Key things to assess include:
- Supplier selection processes and criteria.
- Monitoring and reviewing supplier performance.
- Ensuring that purchased materials and components are compliant with required specifications.
- Proper supplier audits and assessments to evaluate supplier capabilities.
7. Addressing Customer-Related Processes (Clause 8.2.1)
Finally, an ISO 13485 audit checklist must address customer-related processes, as customer satisfaction and feedback are crucial to the ongoing improvement of your QMS. During the audit, evaluate:
- The methods used for capturing customer feedback and complaints.
- Implementing customer requirements into design and production processes.
- Dealing with customer complaints and non-conformances are handled, investigated, and resolved.
- Identifying if customer satisfaction data is analyzed to improve product quality and service delivery.
8. Maintaining Documentation and Records (Clause 4.2)
Proper documentation and record-keeping are fundamental under ISO 13485. The checklist should evaluate whether your organization’s documents and records are well-organized, current, and available for review when needed. Consider these aspects during the audit:
- Adequacy of document control procedures to ensure documents are reviewed and approved.
- Method in which documents are stored and maintained for easy retrieval and traceability.
- Identifying whether records support compliance with regulatory and customer requirements.
- Proper retention of records to meet the mandated timeframes.
Ensure your documents are always in order with BPRHub’s Document Hub, which makes record-keeping and retrieval effortless!
Now that you have understood the effective components of the ISO 13485 audit checklist let's learn the steps to create one.
How to Create an ISO 13485 Internal Audit Checklist?
Creating an ISO 13485 internal audit checklist for internal audits involves several key steps to ensure your quality management system (QMS) is compliant and effective. Here’s a simple breakdown of the process:
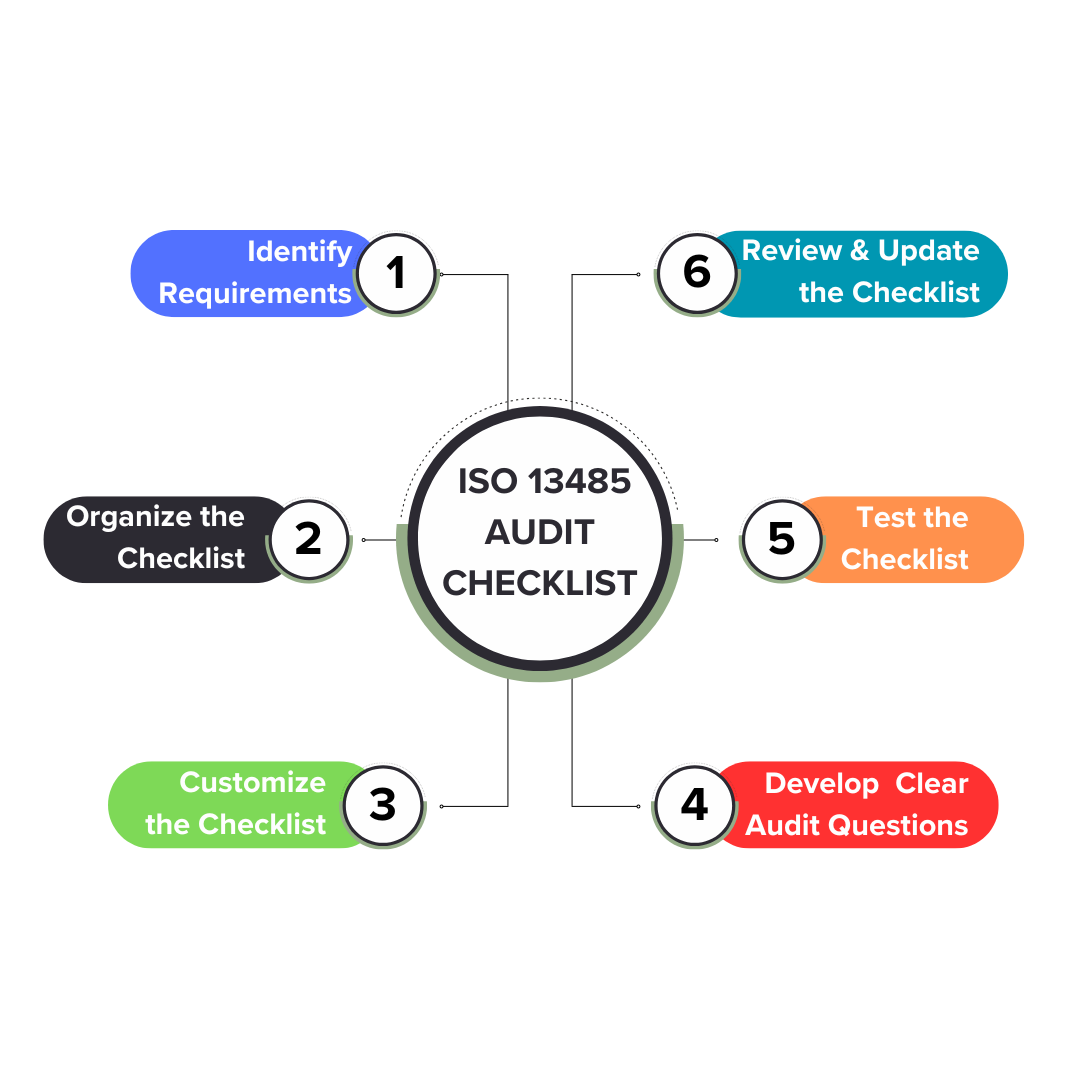
1. Understand ISO 13485 Requirements
Start by familiarizing yourself with the ISO 13485 standard. This includes understanding the core principles related to product design, development, production, and post-market activities. Review the requirements for each area and ensure you’re clear on what needs to be audited, including documentation, process controls, and corrective actions.
2. Organize the Requirements into a Checklist
Once you’ve understood the ISO 13485 requirements, organize them into a structured checklist. Break down each requirement into actionable steps and sections, covering all critical areas such as design controls, purchasing controls, and CAPA. Group the criteria logically so auditors can easily follow the process, ensuring nothing is overlooked.
3. Identify the Key Audit Criteria to Customize the Checklist
Identify the key audit criteria based on the specifics of your business and your QMS. This involves tailoring the checklist to focus on processes like management responsibility, product realization, and resource management. Customizing the checklist ensures it’s relevant to your organization’s operations while covering all mandatory areas outlined by ISO 13485.
4. Develop Clear, Actionable Audit Questions
Craft clear and actionable audit questions that are specific and measurable. Questions like "Is CAPA implemented correctly?" or "Are design reviews documented and compliant?" make it easier for auditors to assess compliance and identify non-conformities. Avoid vague questions, and make sure each one leads to an actionable outcome for process improvement.
5. Test the Checklist & Assign Responsibilities
Before finalizing the checklist, test it with a mock audit or pilot review. This helps you identify any gaps or unclear sections in the checklist. During this process, assign responsibilities to specific team members or departments, ensuring accountability and that each audit area is thoroughly assessed. This ensures a smooth audit flow.
6. Review, Update, and Maintain the Checklist
ISO standards evolve, so it’s crucial to review and update your checklist regularly. Track changes in ISO 13485, adapt to new processes or regulations and update the checklist accordingly. Regular reviews ensure that the checklist remains effective and relevant for ongoing audits, helping maintain consistent compliance with the latest industry standards.
Get a free consultation with BPRHub’s Standard Hub to effortlessly track changes in ISO 13485 and keep your audit checklist always up to date!
Creating a suitable ISO 13485 audit checklist for internal audits may seem like a tedious process, but its significance becomes clear when you consider its numerous benefits. The following session highlights these advantages, showcasing why an effective checklist is essential.
What are the Benefits of Using a Checklist During Internal Audits?
Using an ISO 13485 audit checklist for internal audit can significantly streamline your audit process and ensure a thorough evaluation of your quality management system (QMS). Here’s why incorporating a checklist into your internal audits is a smart move:
- Ensures Comprehensive Coverage
A checklist ensures that no critical area of your QMS is overlooked, guiding auditors through all necessary sections like design controls, production processes, and corrective actions. - Promotes Consistency and Objectivity
It brings consistency by setting clear criteria for evaluation, ensuring that audits are objective and based on measurable facts, and making it easier to compare results over time. - Saves Time and Increases Efficiency
The checklist streamlines the audit process, reducing the time spent figuring out the next steps and allowing auditors to focus on reviewing processes in detail. - Helps with Compliance
Using a checklist helps confirm that all ISO 13485 regulatory requirements are being met and identifies areas where your organization may need corrective action. - Supports Continuous Improvement
The checklist makes it easier to track corrective actions from previous audits, ensuring that issues are addressed and improvements are being implemented. - Improves Communication
With everything documented in the checklist, findings are clearer and easier to communicate, ensuring that all relevant stakeholders understand the audit results and corrective actions. - Enhances Employee Accountability
A checklist assigns clear responsibilities, making it easier to track who is accountable for each part of the audit and ensuring follow-through on corrective actions. - Facilitates External Audits
A well-maintained internal checklist makes the external audit process smoother, as auditors can easily track your internal audit history and see your commitment to compliance.
Using an ISO 13485 audit checklist brings clarity and structure to your internal audits, making the process more efficient and comprehensive. To further elevate this efficiency and simplify compliance management, integrating advanced QMS tools like BPRHub can make a significant difference. Let’s explore how BPRHub enhances the audit process.
Crafting the Ultimate ISO 13485 Audit Checklist with BPRHub
A well-crafted ISO 13485 audit checklist not only ensures that every aspect of your QMS is covered but also promotes consistency, efficiency, and transparency during audits.BPRHub simplifies the process with its Audit Hub feature, allowing you to track, schedule, and execute internal audits seamlessly. This tool enables you to create customizable checklists tailored to your organization's needs, ensuring every critical area of your QMS is covered.
With real-time analytics, BPRHub identifies areas for improvement during audits and provides instant access to compliance status across your operations. Additionally, BPRHub automates complex compliance tasks, streamlining workflows and reducing manual effort. By using BPRHub, you can enhance audit efficiency, improve product quality, and maintain consistent ISO 13485 compliance.
Simplify your ISO 13485 audits and boost compliance—try BPRHub’s Audit Hub today!
FAQ’s
1. What is the ISO 13485 audit checklist?
Ans: An ISO 13485 audit checklist is a tool used to ensure your quality management system (QMS) complies with ISO 13485 standards. It helps auditors evaluate processes, identify gaps, and confirm regulatory adherence. This checklist is essential for maintaining product quality, regulatory compliance, and improving operational efficiency in the medical device industry.
2. How do I create an ISO 13485 audit checklist?
Ans: To create a checklist, first understand ISO 13485 requirements, then organize them into actionable steps. Customize it to focus on your organization's unique processes and ensure clear, measurable audit questions. Regularly test, update, and assign responsibilities to keep the checklist effective and relevant.
3. How does BPRHub simplify the audit process?
Ans: BPRHub simplifies the audit process by centralizing audit management, enabling easy scheduling, tracking, and execution of both internal and external audits. Its real-time compliance checking offers instant access to compliance status, while customizable checklists ensure targeted, efficient audits, streamlining processes and reducing administrative burden for manufacturers.
4. Why is management involvement important in the audit process?
Ans: Management is crucial for supporting QMS implementation, reviewing audit results, and ensuring corrective actions are taken. Their involvement is required under ISO 13485 to evaluate the effectiveness of the QMS and provide resources for continuous improvement.
5. Can I customize my audit checklists with BPRHub?
Ans: Yes, BPRHub allows you to create and customize audit checklists tailored to your specific operational and regulatory needs. This ensures that audits are thorough, targeted, and cover all critical areas, improving audit precision and effectiveness.