Did you know that thousands of workers in the glass manufacturing industry face severe health risks, with many developing life-threatening illnesses due to inadequate safety measures and risk management? In fact, as per a report by Glassforum, exposure to silica dust—a common hazard in glass production—has been linked to serious respiratory diseases like silicosis and lung cancer, affecting a significant portion of the workforce.
Glass manufacturing, while crucial to many industries, requires a thorough glass manufacturing risk assessment to mitigate significant hazards. From handling sharp materials to exposure to harmful chemicals, workers face various hazards daily. Glass manufacturing is an intense process that involves serious risks at every step. Each step of the glass manufacturing process brings unique risks that need careful management to keep workers safe.
From extreme heat and molten glass to sharp fragments and hazardous silica dust, understanding these dangers is crucial. Let’s now take a closer look at these specific hazards and explore effective strategies for minimizing risks and ensuring a secure, efficient work environment.
Common Hazards in Glass Manufacturing
Glass manufacturing presents several hazards that can affect the safety of workers if not properly managed. From physical risks like cuts and burns to chemical exposures and ergonomic challenges, each step of the process carries potential dangers. The U.S. Bureau of Labor Statistics provides detailed data on workplace injuries and illnesses specific to the glass industry. For instance, in 2021, the flat glass manufacturing sector reported 3.2 total recordable cases per 100 workers.
Understanding these common hazards is essential for creating a safer work environment, minimizing accidents, and ensuring compliance with industry safety standards. By recognizing and addressing these risks, manufacturers can not only protect their employees but also improve operational efficiency.
In this blog, we’ll break down the most common hazards you’ll encounter, including:
- Physical Hazards: Think of burns, cuts, and injuries from heavy machinery or lifting.
- Chemical Hazards: Like silica dust, harmful fumes, and even asbestos in older facilities.
- Ergonomic and Noise Hazards: Strains from repetitive tasks, awkward workspaces, and constant exposure to loud machinery.
By the end, you’ll have a clear picture of what to watch out for and how to tackle these risks head-on. Let’s start with the physical hazards.
Physical Hazards
Physical hazards are among the most common risks in glass manufacturing, where the use of heavy machinery, sharp materials, and high temperatures can pose serious dangers to workers.
From burns and cuts to strains and puncture wounds, these hazards can lead to severe injuries if proper safety measures aren't followed. A comprehensive glass manufacturing risk assessment is essential to identify physical hazards and implement effective prevention strategies.
- Injuries from Machinery and Hot Glass: Working with heavy machinery and hot glass can result in serious injuries, including burns, cuts, and punctures. For example, attempting to move large glass sheets without the proper equipment can lead to severe cuts or puncture wounds. Implementing correct handling techniques and using the right tools are key to preventing these types of accidents.
- Burns from Furnaces and Steam: The high temperatures involved in glass manufacturing, especially from furnaces and steam, create significant burn risks. Direct contact with hot surfaces or accidental exposure to steam can cause severe burns. Workers should always follow safety protocols, including wearing appropriate protective gear, to minimize these dangers.
- Strains from Lifting Heavy Objects: Manual lifting of heavy glass materials can cause musculoskeletal injuries, particularly strains in the back, shoulders, and arms. Without proper lifting techniques and assistance devices, workers are at risk of serious strain-related injuries. Ergonomic practices and equipment like lifts or hoists can greatly reduce these risks.
Chemical Hazards
Chemical hazards in glass manufacturing can pose significant health risks to workers, especially when handling or being exposed to harmful substances like silica dust, fumes from solvents, and other hazardous chemicals.
Without the right protective measures, these chemicals can lead to respiratory problems, skin irritation, and long-term health issues. Identifying and mitigating chemical hazards is essential for ensuring a safe working environment and protecting employees from potential harm.
Silica Dust Inhalation
- Inhaling silica dust generated during glass cutting, grinding, and other processes poses serious respiratory risks.
- Continuous exposure can lead to silicosis, a debilitating lung disease caused by the accumulation of fine silica particles in the lungs.
- Without proper protective measures, like masks or effective ventilation systems, workers face long-term health complications.
- The Occupational Safety and Health Administration (OSHA) offers comprehensive guidelines on managing silica dust exposure, a significant concern in glass manufacturing.
Exposure to Chemical Fumes
- Chemicals used in glass manufacturing, such as solvents, adhesives, and coatings, can release harmful fumes into the air.
- Inhaling these fumes in high concentrations can cause respiratory irritation, headaches, dizziness, and long-term health problems.
- Poor ventilation increases the risks, and continuous exposure without proper equipment like respirators can lead to chronic respiratory conditions.
In glass manufacturing, exposure to chemicals like ethylene and silane poses significant risks due to their variable flow characteristics.
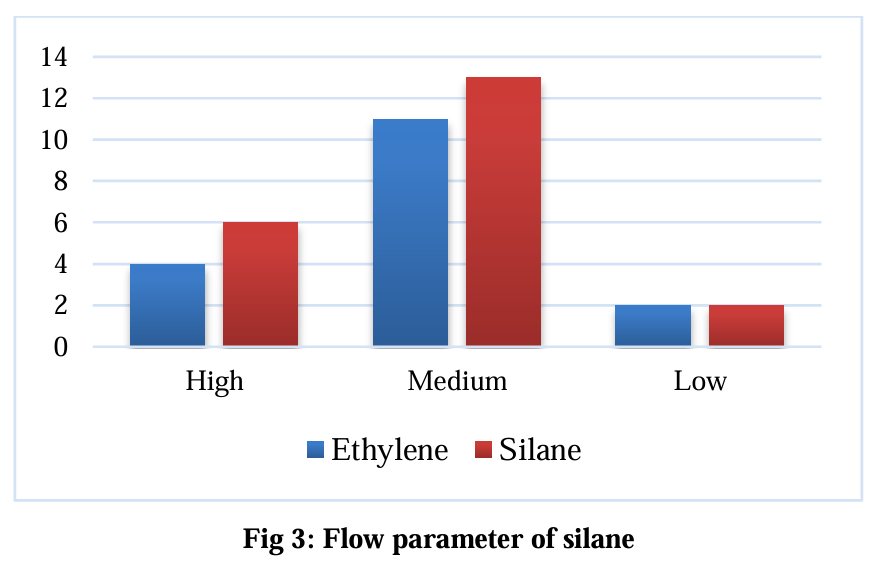
As shown in the chart above, silane demonstrates a higher flow rate under medium conditions, increasing the potential for accidental inhalation or contact during processing. Proper ventilation and protective equipment are essential to mitigate these risks.
Asbestos Exposure
- Although asbestos use has decreased, it may still be present in older manufacturing facilities and equipment.
- Exposure to asbestos fibers can lead to serious health risks, including diseases like asbestosis, lung cancer, and mesothelioma.
- Even low levels of exposure over time can be dangerous, so workers in older buildings must take precautions and undergo regular health screenings to detect early signs of asbestos-related diseases.
Ergonomic and Noise Hazards
Ergonomic and noise hazards are often overlooked in glass manufacturing but can lead to serious long-term health issues. Poorly designed workspaces and repetitive tasks can cause musculoskeletal injuries, while constant exposure to loud machinery may result in hearing loss.
Addressing these hazards with proper ergonomic setups and adequate hearing protection is vital to safeguarding workers' well-being and ensuring a more comfortable and productive working environment.
- Repetitive Motion Injuries: Repeated movements in glass manufacturing, such as lifting, cutting, or grinding, can lead to strain injuries over time. These injuries often affect the joints and muscles, causing long-term discomfort if not addressed with proper ergonomics or breaks.
- Poorly Designed Workspaces: Workspaces that aren’t designed with ergonomics in mind can force workers into awkward postures or movements. This increases the risk of musculoskeletal injuries, emphasizing the need for better workplace layouts and adjustable tools.
- High Noise Levels: Consistent exposure to loud machinery without adequate hearing protection can lead to hearing loss over time. Providing workers with proper hearing protection, like earplugs or earmuffs, is crucial to prevent long-term damage.
Workplace injuries not only affect the well-being of employees but also impose a significant financial burden on businesses. According to the National Safety Council, the average cost per injury is $40,000, including medical expenses and lost productivity.
Prioritizing safety in glass manufacturing is essential not just for protecting workers, but also for maintaining operational efficiency and reducing these costly setbacks.
Now that we've covered the common hazards in glass manufacturing, it's important to focus on how these risks can be effectively prevented. By implementing key safety practices, you can significantly reduce the likelihood of incidents and create a safer work environment.
Emergency Response and Preparedness
Beyond preventing hazards, a glass manufacturing risk assessment can guide the development of an effective emergency response plan. FEMA guidelines highlight the need for tailored emergency procedures, clear roles during crises, and accessible emergency equipment like fire extinguishers and first-aid kits.
Here's how to enhance your emergency preparedness:
- Developing Emergency Response Plans: Every workplace should have clear, actionable emergency response plans for situations like fires, injuries, or other emergencies. These plans help ensure that employees know exactly what to do in a crisis.
- Conducting Regular Drills and Training: Regular emergency drills, such as fire evacuations or medical response training, keep employees prepared for unexpected incidents. Practice makes sure that workers can react quickly and safely.
- Establishing Clear Communication Protocols: Effective communication during emergencies is crucial. Make sure your team knows how to quickly report incidents and contact the necessary emergency services. Having designated communication channels can prevent confusion and ensure timely responses.
While many over-pressurization incidents in glass manufacturing facilities may not immediately exceed levels of concern, preparedness for such emergencies is essential. The table below illustrates how different vapor cloud scenarios and hole sizes influence the threat zones.
Proper emergency response protocols, including timely evacuation and containment measures, are critical in preventing potential incidents from escalating, even when LOC levels are not exceeded.
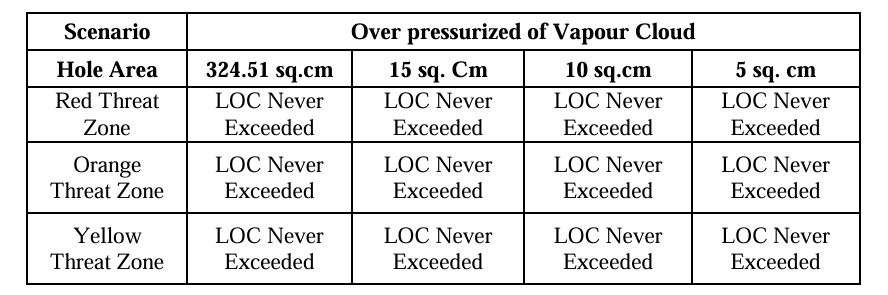
Prioritizing safety and preparedness not only keeps your team safe but also ensures smooth, uninterrupted workflows.
Concerned about your current safety protocols? Our platform automates critical safety tasks, provides real-time safety tracking, and helps you stay ready for any situation. Reach out today for a free consultation and see how BPRHub can make your glass manufacturing operations safer and more resilient.
Incident Prevention and Safety Practices
Preventing incidents in glass manufacturing requires a proactive approach to safety. By implementing effective safety practices, employers can significantly reduce the risk of accidents and create a safer work environment.
From using personal protective equipment (PPE) to maintaining machinery and providing comprehensive training, these practices are essential for minimizing hazards and ensuring the well-being of workers. Let's explore some key strategies for preventing incidents and promoting safety in glass manufacturing.
Key Strategies for Incident Prevention
- Comprehensive Safety Training: Regular and thorough safety training ensures that workers are aware of potential hazards and the necessary precautions to take. This includes training on proper glass handling techniques, machinery operation, and emergency response procedures.
- Use of Personal Protective Equipment (PPE): Equipping workers with appropriate PPE—such as gloves, safety glasses, hearing protection, and respiratory masks—can significantly reduce the risk of injuries. For example, using cut-resistant gloves can prevent hand injuries when handling glass.
- Regular Equipment Maintenance: Regularly inspecting and maintaining machinery and tools is essential to prevent malfunctions that can lead to accidents. Proper maintenance ensures equipment operates safely and reduces the likelihood of unexpected breakdowns.
- Effective Supervision: Competent supervision plays a key role in enforcing safety protocols and quickly addressing any hazards that arise. Attentive supervisors ensure that safety measures are consistently followed, minimizing the risk of accidents.
- Comprehensive Safety Audits: Conducting regular safety audits helps identify risks that might otherwise go unnoticed. From outdated machinery to improper use of tools, these audits ensure compliance and workplace safety.
- Proper Workspace Layout: Ergonomic designs should be integrated into workspaces to minimize strain. This includes arranging tools within easy reach and adjusting workstations to the height and movement needs of individual workers.
- Employer Responsibility: Employers must take a proactive approach to safety training by providing access to up-to-date safety courses. This ensures employees are prepared to handle the risks associated with glass manufacturing.
- Encouraging Continuous Learning: In industries like glass manufacturing, where technology and techniques evolve, continuous learning helps prevent complacency. Employees should feel encouraged to refresh their knowledge and engage in advanced training, especially in areas such as handling hazardous chemicals or operating new machinery.
Importance of Ongoing Safety Training
Continuous safety training is vital in reinforcing safe practices and updating workers on new hazards or procedures. It fosters a culture of safety and empowers employees to make informed decisions in their daily tasks. Recognizing and addressing the various hazards in glass manufacturing is key to creating a safe and efficient work environment.
Implementing comprehensive safety measures and fostering a culture of continuous improvement can significantly reduce risks associated with glass manufacturing processes. Continuous safety training is vital in reinforcing safe practices and updating workers on new hazards or procedures. It fosters a culture of safety and empowers employees to make informed decisions in their daily tasks.
BPRHub’s Compliance Hub is your go-to solution for managing ongoing safety training efficiently. With automated compliance tracking and real-time updates on safety protocols, you can ensure that your team stays informed and practices are consistently reinforced. Contact us to learn how we can help you streamline safety training and keep your workplace secure!
FAQ’s
1. What are the primary hazards associated with glass manufacturing?
Glass manufacturing involves several hazards, including:
- Physical Injuries: Cuts from sharp edges, burns from hot materials, and crush injuries from heavy glass sheets.
- Chemical Exposure: Inhalation of dust and fumes from raw materials and chemicals used in production.
- Ergonomic Risks: Musculoskeletal disorders from repetitive motions and manual handling of heavy items.
- Noise Exposure: Hearing damage due to prolonged exposure to high noise levels from machinery.
2. How can workers protect themselves from cuts and lacerations?
To minimize the risk of cuts:
- Wear Appropriate PPE: Use cut-resistant gloves, safety glasses, and protective clothing.
- Handle Glass Properly: Use correct lifting techniques and avoid carrying glass under the arm or above the head.
- Maintain a Clean Workspace: Keep areas free of broken glass and debris.
3. What measures can reduce chemical exposure in glass manufacturing?
To mitigate chemical exposure:
- Implement Ventilation Systems: Ensure proper ventilation to disperse harmful fumes.
- Use Respiratory Protection: Provide masks or respirators when handling hazardous substances.
- Conduct Regular Training: Educate employees on safe handling and emergency procedures.
4. How can ergonomic risks be managed in the workplace?
To address ergonomic hazards:
- Provide Training: Educate workers on proper lifting techniques and posture.
- Use Mechanical Aids: Employ equipment like hoists and conveyors to reduce manual handling.
- Design Workstations Ergonomically: Adjust workstations to minimize strain and repetitive motions.
5. What steps can be taken to protect workers from noise exposure?
To safeguard against noise-induced hearing loss:
- Conduct Noise Assessments: Regularly measure noise levels in the facility.
- Provide Hearing Protection: Supply earplugs or earmuffs to employees.
- Implement Engineering Controls: Install noise barriers or dampening materials around loud equipment.
6. How important is personal protective equipment (PPE) in glass manufacturing?
PPE is crucial as it provides a barrier between workers and potential hazards, significantly reducing the risk of injuries and illnesses. Proper selection, use, and maintenance of PPE are essential for effective protection.
7. What role does training play in ensuring safety in glass manufacturing?
Training is vital for:
- Hazard Awareness: Educating employees about potential risks.
- Safe Work Practices: Teaching correct procedures and use of equipment.
- Emergency Preparedness: Preparing workers to respond effectively to incidents.
8. How can employers ensure compliance with safety regulations?
Employers can:
- Stay Informed: Keep up-to-date with relevant safety standards and regulations.
- Conduct Regular Audits: Perform safety inspections and assessments.
- Engage Employees: Encourage reporting of hazards and participation in safety programs.
9. What are the consequences of neglecting safety in glass manufacturing?
Neglecting safety can lead to:
- Increased Injuries: Higher incidence of workplace accidents.
- Legal Penalties: Fines and sanctions from regulatory bodies.
- Reduced Productivity: Operational disruptions due to accidents.
- Damage to Reputation: Loss of trust from clients and employees.
10. How can a safety culture be fostered in a glass manufacturing facility?
To cultivate a safety culture:
- Lead by Example: Management should prioritize and model safe behaviors.
- Encourage Communication: Promote open discussions about safety concerns.
- Recognize Safe Practices: Acknowledge and reward adherence to safety protocols.
- Provide Continuous Education: Offer ongoing training and development opportunities.
Understanding and addressing the risks in glass manufacturing is essential for creating a safe and productive work environment. Implementing comprehensive safety measures protects employees and enhances overall operational efficiency.