In the aerospace industry, a single defect can lead to disastrous consequences, with the global aerospace industry spending over $3 billion annually on quality management alone. AS9100 is the industry benchmark for quality management and plays a vital role in ensuring top-tier production standards and regulatory compliance.
Among its key components, Clause 8.4.3 stands out as it governs the control of external providers, ensuring that every part of the supply chain meets rigorous standards. But why is this control so essential?
Let’s examine the details of AS9100 clause 8.4.3 and explore how to stay ahead in a highly competitive and safety-critical industry.
An Overview of AS9100 8.4.3
In the world of aerospace manufacturing, maintaining high standards is non-negotiable. AS9100, a widely adopted quality management standard, helps organizations ensure that their processes meet both customer and regulatory requirements. One critical component of AS9100 is Clause 8.4.3, which focuses on the Control of External Providers. But what does this actually mean? Let’s break it down.
What is AS9100 8.4.3?
AS9100 8.4.3 outlines the requirements for controlling external providers or suppliers involved in the production of aerospace components.
External providers are essentially companies or individuals outside your organization who provide materials, services, or components critical to the product you’re delivering. This clause ensures that these external entities also meet the strict quality standards required in the aerospace industry.
The main idea behind clause 8.4.3 is that you must have a structured approach to select, monitor, and evaluate your external providers to ensure the quality and safety of the end product.
Why is Control of External Providers Important?
In aerospace, any failure to meet quality standards can have catastrophic consequences. That’s why controlling external providers is crucial. These suppliers play a pivotal role in maintaining the integrity of the entire supply chain. A subpar supplier can lead to defects, delays, and increased costs, all of which can damage your reputation and, more importantly, compromise safety.
By implementing the control measures outlined in 8.4.3, you can ensure that each external provider aligns with your organization’s quality expectations and regulatory requirements. This oversight helps minimize risk and ensures that you are delivering safe, reliable products to your customers.
To ensure compliance with AS9100 8.4.3 and maintain high standards, it's essential to not only communicate clear requirements but also establish a system for ongoing monitoring and performance evaluation. Let’s now explore the key aspects of managing and controlling external providers.
Key Aspects of AS9100 8.4.3: Control of External Providers
AS9100 8.4.3 lays out several key requirements for managing and communicating expectations to external providers. These requirements help create a clear framework for quality control and consistent supplier performance.
1.Clear Communication of Requirements
Before an external provider begins work, it’s crucial to ensure that the requirements for the product or service are fully understood. This includes specifying relevant technical data (e.g., drawings, specifications, process requirements), approval methods, and any quality expectations. The organization must communicate exactly what is needed for both the process and product to be acceptable.
2.Approval Requirements
The organization must convey its approval requirements to external providers regarding certain topics. They are:
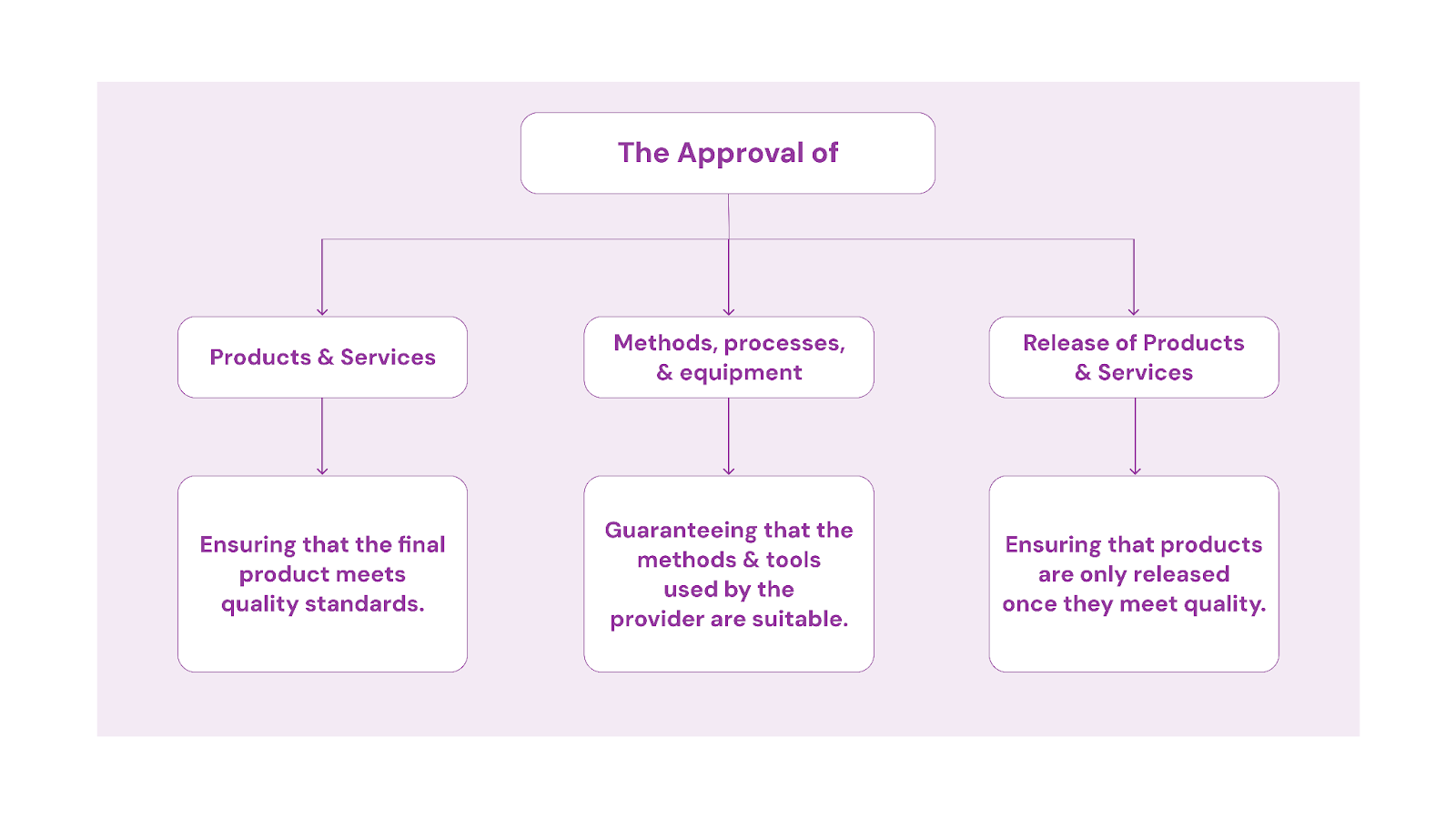
3.Competence and Qualification
The organization must specify any qualifications or competencies required for the provider’s personnel. This ensures that the provider has the necessary expertise to meet quality standards and handle the critical aspects of the aerospace production process.
4.Monitoring and Control of Performance
Ongoing monitoring of an external provider’s performance is essential. This includes assessing their adherence to contractual requirements, delivery schedules, and quality standards. The organization must have clear methods in place for evaluating the provider’s performance and implementing corrective actions if necessary.
Simplify performance monitoring with BPRHub’s Standard Hub, offering real-time tracking, contract compliance, and easy evaluation of your external providers.
5.Verification and Validation Activities
The organization or its customer may need to carry out verification or validation activities at the external provider’s premises. These activities help ensure that the processes and products are being carried out to the specified standards and allow for corrective actions if deviations are found.
6.Special Requirements and Critical Characteristics
Some products or services may require special attention, such as specific critical characteristics, testing, or validation. AS9100 8.4.3 outlines how these special requirements should be communicated to the external provider, ensuring that they understand their importance and the steps they need to follow.
7.Prevention of Counterfeit Parts
AS9100 8.4.3 requires that organizations ensure that external providers are aware of the need to prevent counterfeit components from being used in their processes. This is critical to ensuring the safety and reliability of the final product.
8.Changes to Processes or Products
Any changes to the processes, products, or services provided by the external provider must be communicated to the organization. This includes changes in the provider’s location, manufacturing processes, or even their suppliers. Prior approval is necessary before making these changes.
9.Access to Facilities and Documentation
AS9100 8.4.3 ensures that the organization, its customers, and regulatory authorities have the right to access the external provider’s facilities and any relevant documentation. This is crucial for auditing and verifying compliance with the set quality standards.
For a seamless documentation process, get started with BPRHub’s document hub feature.
10. Ethical Behavior and Product Safety
Finally, 8.4.3 stresses the importance of ethical behavior and the awareness of personnel regarding their roles in ensuring product conformity and safety. Every individual involved in the process must understand their contribution to both the product’s quality and its safety.
What Are the Challenges in As9100 8.4.3 Implementation?
This clause is designed to ensure that all suppliers meet the high-quality standards required for aerospace manufacturing, but translating these requirements into effective processes can be complex. Here are some of the key challenges that organizations often face when implementing this clause:
- Supplier Evaluation and Selection: Finding and selecting external providers that meet aerospace standards requires thorough risk assessments and compliance checks, which can be time-consuming and resource-heavy.
- Managing Supply Chain Complexity: The multi-tiered aerospace supply chain demands robust tracking and communication systems, which are challenging to maintain across diverse and geographically dispersed suppliers.
- Monitoring and Auditing Suppliers: Continuous monitoring and regular audits of external providers are necessary to ensure compliance and prevent potential non-conformances, which adds to operational costs.
- Risk Management: Effective risk assessments for external providers can be challenging, especially when working with new or untested suppliers. Determining appropriate mitigation strategies is critical to maintaining quality and compliance.
- Control of Changes: Managing and assessing changes in processes, materials, or delivery schedules from external providers is crucial to prevent negative impacts on product quality, safety, and delivery timelines.
Despite the challenges in implementing AS9100 8.4.3, clarifications from the International Aerospace Quality Group (IAQG) provide valuable insights and flexibility. The IAQG recognizes that each organization’s context may differ, allowing for tailored approaches to meet compliance.
For example, allowances can be made for smaller organizations or unique situations where certain requirements may not be fully applicable or must be adjusted based on the scope and scale of operations. By leveraging these clarifications and allowances, organizations can adopt a more pragmatic approach to implementing Clause 8.4.3, ensuring both compliance and operational efficiency.
Let’s understand the ways to handle these challenges and how risk assessment and clear communication can help manage them effectively.
How to Handle Challenges and Risk Assessments Provided in AS9100 8.4 3?
Effectively managing external providers comes with several challenges, particularly in risk assessments and controlling changes to externally provided elements. Below is a guide on how to tackle these challenges:
Processes for Controlling Changes to Externally Provided Elements
In the aerospace industry, changes to materials, processes, or external suppliers’ methods can significantly impact the final product. AS9100 8.4.3 requires a clear and structured process for controlling changes to externally provided elements to ensure that these changes do not compromise quality, safety, or regulatory compliance.
Here are steps to effectively control changes:
- Establish a Change Management Process: Set up clear procedures for communicating and documenting any changes in external providers’ processes, materials, or delivery timelines. This helps to mitigate the risks associated with unexpected modifications, ensuring that all stakeholders are informed and can take appropriate action.
- Assess the Impact of Changes: Every change introduced by external providers should undergo an impact analysis. This involves reviewing how the change might affect quality, cost, delivery schedules, and compliance with industry standards. Engage with relevant internal departments (quality, engineering, compliance) to evaluate the risk posed by the change.
- Monitor the Implementation of Changes: Once a change is approved, ensure that external providers implement the change according to the agreed-upon plan. Regular monitoring, inspections, or audits can help verify that the change has been properly integrated and doesn’t introduce new risks into the supply chain.
Companies can prevent disruptions and ensure consistent product quality by rigorously controlling changes. Risk assessment plays a crucial role in this process, helping to identify potential issues before they arise. Let’s explore the importance of risk assessment in managing external providers effectively.
The Importance of Risk Assessments and Rationale in Communication Decisions
Risk assessments are a core component of Clause 8.4.3 and are vital in managing external providers. These assessments help identify potential threats, gauge their severity, and plan mitigation strategies. However, equally important is ensuring that the rationale behind risk decisions is effectively communicated to all parties involved. Here’s why:
- Clear Decision-Making: Conducting a thorough risk assessment allows you to make informed decisions about whether to accept or reject certain risks from external providers. This process helps identify the most critical areas that could impact the product’s integrity, safety, or compliance.
- Building Trust with External Providers: If a risk is identified and a particular decision (such as switching suppliers or implementing stricter quality checks) is made, providing a clear explanation helps external providers understand your reasoning and act accordingly.
- Improved Supplier Relationships: When risk assessments and their associated decisions are communicated effectively, suppliers are more likely to take proactive measures to address any concerns. By clearly stating the importance of specific risk factors—such as product conformity or timely delivery—you set clear expectations and foster better cooperation in managing those risks.
- Documentation for Compliance: In aerospace, proper documentation of risk assessments and their rationale is essential for compliance purposes. If a quality issue arises, having a well-documented record of the risk assessment process and the reasoning behind decisions helps demonstrate compliance with AS9100 standards during audits or regulatory reviews.
Implementing tools like BPRHub, which automate tedious tasks and provide real-time insight, is essential for effectively managing external providers and meeting the rigorous requirements of AS9100 8.4.3.
BPRHub: Your Trusted Partner in External Provider Control
As we understand, controlling external providers is critical for quality and compliance in aerospace manufacturing. AS9100 8.4.3 outlines the key requirements for this, but managing it can be challenging. BPRHub simplifies the process, ensuring compliance and minimizing risks like quality issues and delays.
BPRHub is a cloud-based compliance management platform that ensures all AS9100 8.4.3 requirements are met, from clear communication of technical specifications to monitoring performance and ensuring product safety. By integrating BPRHub, you streamline supplier evaluation, ensure quality consistency, and minimize risks. All while maintaining full visibility and control over your supply chain, you empower yourself to meet and exceed aerospace industry standards.
Get a free consultation to discover BPRHub’s Audit Hub feature—your all-in-one solution for managing compliance, simplifying audit management, and ensuring AS9100 8.4.3 compliance.
FAQ’s
1.What are the key characteristics of AS9100 clause 8.3.4?
Ans: AS9100 Clause 8.3.4 ensures that design and development outputs are documented, meet specified requirements, are suitable for verification and validation, and are traceable to inputs, ensuring consistent, reliable, and compliant product results throughout the process.
2.Can BPRHub support external provider management?
Ans: Yes, BPRHub helps manage external providers by tracking their performance, ensuring they meet quality and regulatory requirements, and providing visibility and control over the supply chain, all in alignment with AS9100 standards.
3.What are the key requirements for controlling external providers under AS9100 8.4.3?
Ans: Key requirements include clear communication of product/service specifications, approval processes, ongoing performance monitoring, and ensuring compliance with special requirements like preventing counterfeit parts and conducting verification activities.
4.How does BPRHub support compliance with AS9100 8.4.3?
Ans: BPRHub simplifies the management of external providers by streamlining documentation, performance monitoring, and approval processes. Features like the Document Hub and Standard Hub help ensure compliance with AS9100 8.4.3, reducing risks and enhancing supply chain efficiency.
5.What is AS9001 certification?
Ans: AS9100 certification is a quality management standard specifically for the aerospace industry. It outlines requirements for consistent product quality, safety, and regulatory compliance and focuses on areas such as design, development, production, and supply chain management.