Maintaining high quality while meeting strict regulatory standards can be a real challenge. With regulations constantly changing, manufacturers must ensure their products not only meet internal quality benchmarks but also comply with industry-specific safety and operational guidelines.
In fact, organizations with a quality management system (QMS) can reduce process costs by 15% and decrease errors by 30%, leading to significant operational improvements.
By implementing standardized protocols, manufacturers can enhance consistency in production, leading to better product quality and compliance.
Additionally, a solid quality management system leverages real-time data to inform decisions, allowing businesses to stay ahead of regulatory requirements. As industries evolve, having a robust quality management strategy is essential for long-term success.
In this blog, we’ll explore what a systematic approach to quality management looks like and how you can implement effective strategies to boost your organization’s operational excellence.
What Does a Systematic Approach to Quality Management Mean?
A systematic approach to quality management is crucial for organizations looking to improve efficiency and maintain high product standards. This method integrates various quality processes to create a cohesive framework that drives continuous improvement.
By focusing on process mapping, effective documentation, and data-driven insights, businesses can streamline operations and ensure compliance with regulations.
Key Pillars of a Systematic Approach
A quality management system (QMS) serves as a comprehensive framework that standardizes and streamlines an organization's processes, ensuring that products or services consistently meet or exceed customer expectations. The systematic approach involves several key steps from concept to delivery, allowing for enhanced control over quality.
- Standardization: Establishing consistent procedures and guidelines across the organization to ensure uniformity in processes and outputs.
- Streamlining Processes: Optimizing workflows to eliminate inefficiencies and reduce waste, making it easier to deliver quality products or services.
- Customer Focus: Prioritizing customer needs and expectations to ensure that products or services not only meet but exceed their requirements.
- Data-Driven Decision Making: Utilizing data and analytics to monitor performance and inform decisions, ensuring that quality improvements are based on evidence.
- Continuous Improvement: Emphasizing a culture of ongoing enhancement where processes are regularly reviewed and refined based on feedback and performance metrics.
- Risk Management: Identifying potential risks and implementing strategies to mitigate them, ensuring the stability and reliability of products or services.
- Documentation and Accountability: Maintaining thorough records of processes, quality controls, and compliance measures to ensure transparency and accountability throughout the organization.
Want to see how leading manufacturers are automating their quality processes? Schedule a personalized demo to discover BPRHub's real-time quality monitoring capabilities.
Foundations of Building a Systematic Approach
Building an effective quality management system requires a strong foundation. These elements ensure a culture of excellence, regulatory compliance, and operational efficiency.
1. Process Mapping for Clarity and Consistency: Mapping out each stage of product or service delivery is crucial. Tools like process flowcharts and value stream mapping help visualize workflows, identify inefficiencies, and integrate quality checks throughout the process—not just at the end. This proactive approach reduces lead times, minimizes errors, and improves overall outcomes.
2. ISO Principles: A Proven Framework: The principles outlined in ISO standards, like ISO 9001, provide a comprehensive framework for quality management:
- Customer Focus: Continuously align efforts with customer expectations.
- Leadership: Set clear direction and unity of purpose.
- Engagement of People: Foster collaboration and individual contributions.
- Process Approach: Standardize activities to achieve predictable outcomes.
- Improvement: Prioritize iterative enhancements.
- Evidence-Based Decisions: Leverage data for informed decisions.
- Relationship Management: Build strong connections with stakeholders.
3. Role of Documentation in Quality and Compliance: Effective documentation is the backbone of quality management. It ensures clarity, accountability, and alignment with regulatory requirements. By maintaining detailed records, organizations simplify audits, foster transparency, and support continuous improvement.
4. Quality Policy and Objectives: A robust quality policy aligned with ISO standards ensures that quality objectives reflect strategic goals. Regular reviews of these objectives help organizations adapt to evolving regulations and market conditions.
Conducting Risk Analysis: Proactively Safeguard Quality
Risk analysis is essential for maintaining product quality and operational success. By identifying and assessing potential risks, organizations can create strategies to mitigate them before they affect performance. This proactive approach enhances reliability and protects reputation.
- Integral to Quality Management: Risk management is a crucial component of quality management systems.
- Identifying Potential Risks: Recognizing risks early helps in assessing their potential impact on product quality.
- Impact Assessment: Evaluating the severity and likelihood of identified risks is essential for prioritizing mitigation strategies.
- Developing Mitigation Strategies: Formulating actionable plans to address and reduce risks is vital for maintaining product quality.
- Proactive Approach: Taking a proactive stance on risk analysis helps avoid regulatory penalties and protects the organization’s reputation.
- Utilizing FMEA: Tools like Failure Mode and Effects Analysis (FMEA) can systematically evaluate potential failure points and guide the implementation of corrective actions.
Don't let quality risks keep you up at night. See how BPRHub's advanced risk assessment tools can protect your operations. Get your free risk analysis.
With the framework in place, it's time to dive into the heart of quality management – your processes. Here's how to take control and drive real results.
Driving Continuous Improvement in Quality Management
Well-defined processes are crucial for achieving consistency and efficiency in operations. By standardizing procedures, organizations minimize variability and ensure that each product or service meets the established quality criteria.
This standardization simplifies training for new employees, enhancing overall productivity. A consistent approach allows for easier scalability as organizations grow. It also provides a foundation for ongoing improvement initiatives, making it easier to identify and eliminate waste.
Continuous Improvement Through Regular Reviews
Continuous improvement should be a core tenet of any QMS. Regular reviews and analyses of processes allow organizations to identify areas for enhancement and foster a culture of innovation. Implementing feedback loops ensures that insights from audits and employee suggestions are integrated into operational practices.
This approach aligns well with methodologies such as Plan-Do-Check-Act (PDCA), which promotes iterative cycles of improvement in the quality management process, enabling organizations to continually refine their practices, enhance efficiency, and respond effectively to changing conditions and stakeholder feedback.
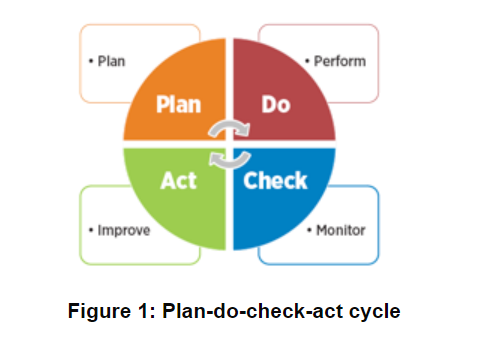
The best systems are only as good as the people behind them. Here's how to transform your team into quality champions.
The Role of Leadership and Culture in Quality Management
Employee engagement and leadership are crucial for the effectiveness of a quality management system (QMS). Engaged employees take ownership of their roles and actively participate in quality initiatives, which enhances productivity and morale. Strong leadership fosters a quality-centric culture by emphasizing the importance of quality and supporting employee involvement.
By investing in training and development, leaders empower their teams to contribute to continuous improvement efforts, ultimately driving better quality performance across the organization.
- Engaging Employees Through Training and Quality Initiatives: Employee engagement is crucial for a successful QMS. Training programs that focus on quality management principles empower employees to take ownership of quality.
Initiatives that recognize and reward quality contributions can further motivate staff, fostering a culture of quality throughout the organization. Engaging employees in quality circles or improvement teams can facilitate collaboration and innovation, leveraging diverse perspectives within the organization.
- Leadership’s Role in Fostering a Quality-Centric Culture: Strong leadership is essential for promoting a quality-centric culture. Leaders must communicate the importance of quality management and actively support initiatives aimed at improving quality.
By setting clear expectations and leading by example, leaders can inspire their teams to prioritize quality. A commitment from top management not only drives resource allocation but also instills a sense of responsibility across all levels of the organization.
While people and process form the backbone of quality management, it's the intelligent use of data that gives you the competitive edge. Let's explore how to make your data work smarter, not harder.
Turning Data into Decisions
Integration and data management are crucial components of a quality management system (QMS), focusing on the seamless flow of quality-related data across the organization. By ensuring robust data collection methods and accessibility, organizations can gain a comprehensive view of their processes and performance metrics.
This facilitates informed decision-making, allowing teams to identify trends, proactively address issues, and implement corrective actions based on real-time insights. Effective data management not only supports compliance with regulatory standards but also drives continuous improvement and enhances overall quality.
- Facilitating the Flow of Quality-Related Data: Effective data management is essential for quality improvement. A systematic approach to data integration ensures that quality-related data flows seamlessly through the organization. This integration facilitates informed decision-making, enabling businesses to respond promptly to quality issues. Data analytics tools can assist in interpreting quality metrics, providing insights that drive performance improvements and strategic decisions.
- Evidence-Based Decision Making: Using data to drive decisions is a hallmark of successful quality management. By collecting and analyzing quality metrics, organizations can make evidence-based adjustments that enhance overall quality. This approach aligns with BPRHub's capabilities in providing real-time compliance data, allowing for swift corrective actions.
Navigating Compliance and Regulatory Standards
Navigating compliance and regulatory standards can feel like a maze, but understanding these requirements is crucial for maintaining quality and protecting your business. Whether you’re in manufacturing, healthcare, or any regulated industry, adhering to standards like ISO 9001:2015 not only helps avoid costly penalties but also enhances your organization’s reputation.
A recent report revealed that over 1.3 million organizations worldwide hold ISO 9001 certification, demonstrating a strong commitment to quality management.
Imagine being able to ensure that your processes consistently meet both internal and external expectations—this is where a solid quality management system (QMS) comes into play. It provides the framework needed to monitor compliance effectively and adapt to changing regulations.
Key Reasons to Prioritize Compliance
- Avoid Costly Penalties: Non-compliance can lead to significant fines and legal issues. Staying informed about regulations helps mitigate these risks.
- Enhance Reputation: Compliance with recognized standards builds trust with customers, partners, and stakeholders, positioning your organization as a leader in quality.
- Improve Operational Efficiency: Implementing compliance measures often streamlines processes, leading to enhanced productivity and reduced waste.
- Foster Continuous Improvement: A commitment to compliance encourages a culture of continuous improvement, helping organizations adapt and thrive in a changing regulatory environment.
Ensuring Compliance with ISO 9001:2015 and Other Relevant Standards
Compliance with ISO 9001:2015 is critical for maintaining quality and credibility. Understanding the nuances of this standard—and other relevant regulations—ensures that organizations can operate within legal parameters while delivering high-quality products or services.
This includes maintaining updated training for employees on compliance standards, and ensuring they are well-versed in both internal and external requirements. Regular training updates are crucial, especially in an environment where industries are increasingly adopting ISO standards—over 552,000 valid ISO 9001 certificates were recorded in China alone as of 2022.
Understanding Specific ISO/IEC Standards
For industries requiring specific certifications, such as ISO/IEC 17025 for laboratories, understanding these standards is vital. Compliance not only mitigates the risk of penalties but also enhances marketability and customer trust.
Benefits of Compliance with ISO/IEC 17025
- Enhanced Marketability: Accreditation signals adherence to internationally recognized standards, providing a competitive edge.
- Increased Customer Trust: Compliance fosters trust among clients, ensuring the reliability of laboratory results.
- Mitigated Risks: Adhering to the standard reduces the risk of errors and potential penalties.
- Improved Operational Efficiency: Streamlined operations lead to increased efficiency and reduced costs associated with rework.
Applications and Benefits of a Systematic Approach
The applications and benefits of a quality management system (QMS) are significant across various industries, including manufacturing and healthcare. Implementing a systematic approach enhances operational efficiency, improves product quality, and ensures regulatory compliance.
Key advantages include reduced costs from streamlined processes, increased customer satisfaction through consistent product delivery, and better risk management that minimizes compliance penalties.
A QMS also promotes a culture of continuous improvement, enabling employees to proactively identify and address quality issues.
- Real-World Industry Applications: Quality management systems have diverse applications across various industries, including automotive, healthcare, and manufacturing. Implementing a systematic approach leads to improved operational performance, waste reduction, and increased customer satisfaction. For instance, the automotive industry utilizes QMS to ensure product safety and reliability, while the healthcare sector focuses on compliance with strict regulations to ensure patient safety.
- Improving Business Performance: A well-implemented QMS can significantly enhance business performance. By reducing errors and optimizing processes, organizations can achieve cost savings, improve turnaround times, and boost overall productivity. This alignment of quality management with business objectives is essential for sustaining competitive advantages.
Ready to see these benefits in action? Join the hundreds of manufacturers who've transformed their quality management with BPRHub. Schedule your personalized demo today.
Unlock Efficiency and Compliance with BPRHub
Adopting a systematic approach to quality management is not just a compliance requirement; it's a commitment to continuous improvement and operational excellence. By integrating BPRHub's advanced compliance management solutions, organizations can automate compliance processes and make data-driven decisions that enhance manufacturing operations.
Still wondering if your current quality management system is holding you back? Don't let complex compliance and quality management slow down your growth. Join industry leaders who've achieved:
- 40% reduction in compliance-related delays
- 65% faster quality documentation process
- 80% decrease in manual quality checks
Ready to revolutionize your quality management? Contact BPRHub today and take the first step toward effortless quality management.